High-performance and Sustainable Battery Cells
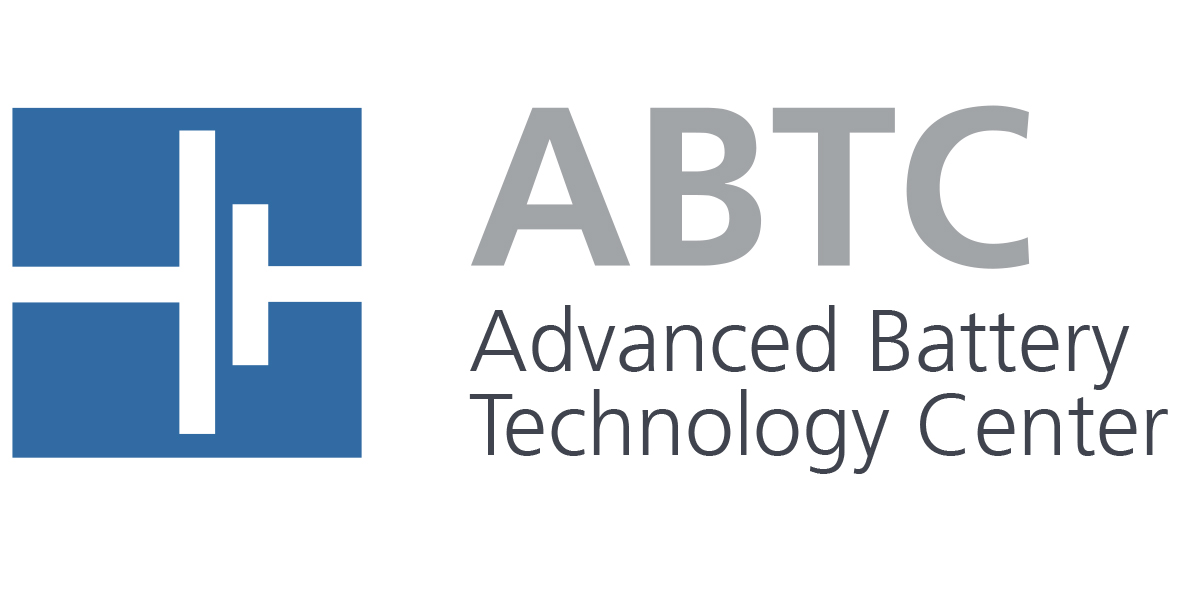
The objectives of the “Advanced Battery Technology Center“ (ABTC) are the development of new materials and innovative technologies for high-performance and sustainable battery cells. Expertise in battery chemistry, innovations in electrode production and modern cell manufacturing technologies are brought together on an interdisciplinary basis.
In the ABTC, researchers from the Technische Universität Dresden (Chair of Inorganic Chemistry I, focus on materials and electrochemistry) work together with Fraunhofer IWS experts in materials, surface and laser technologies under one roof. This team develops new solutions from materials to manufacturing processes to prototype cells and their evaluation. The focus is on lithium-based high-energy cells, such as lithium-ion, lithium-sulfur and solid-state batteries. In this way, the ABTC addresses the holistic process chain for the development of new battery cells and transfers new research results from the laboratory into application-relevant prototypes.