Compact DLIP systems and equipment
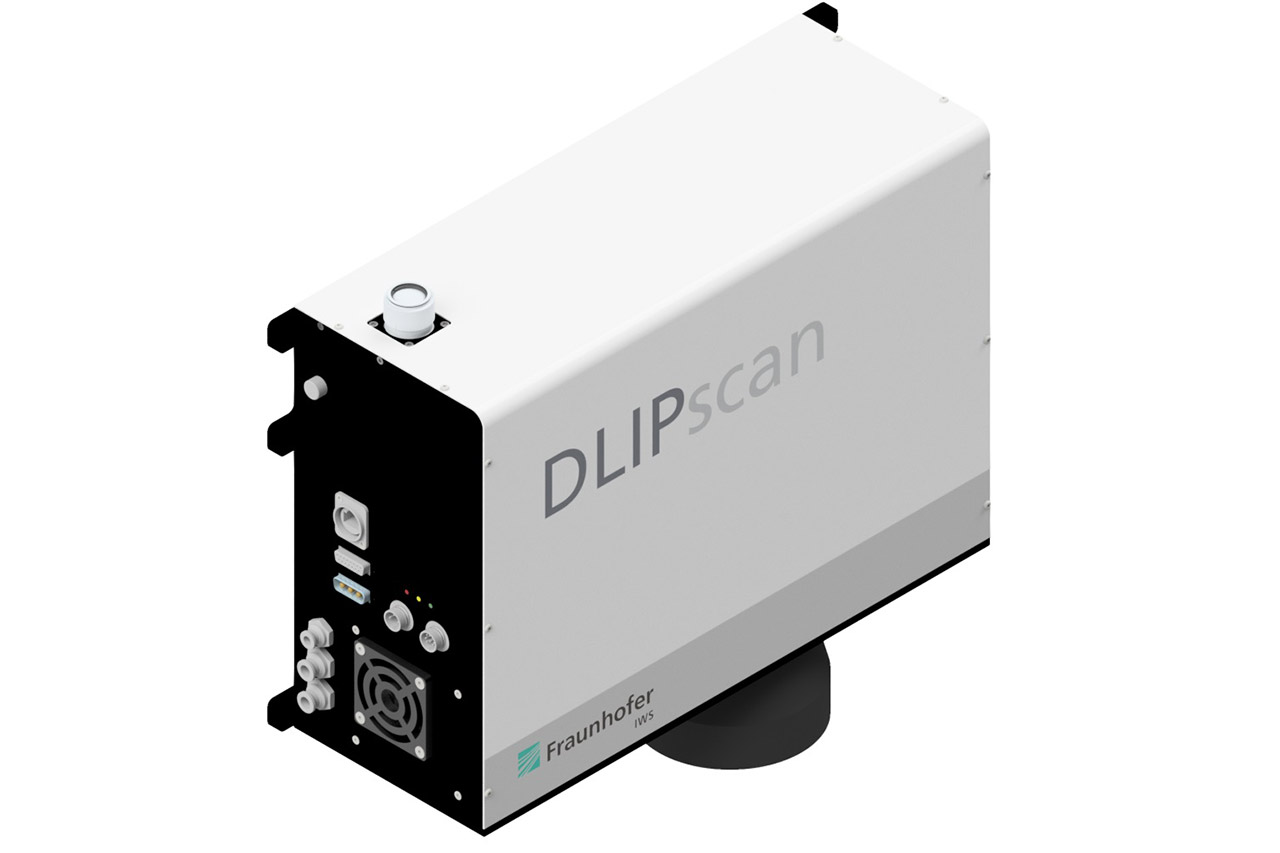
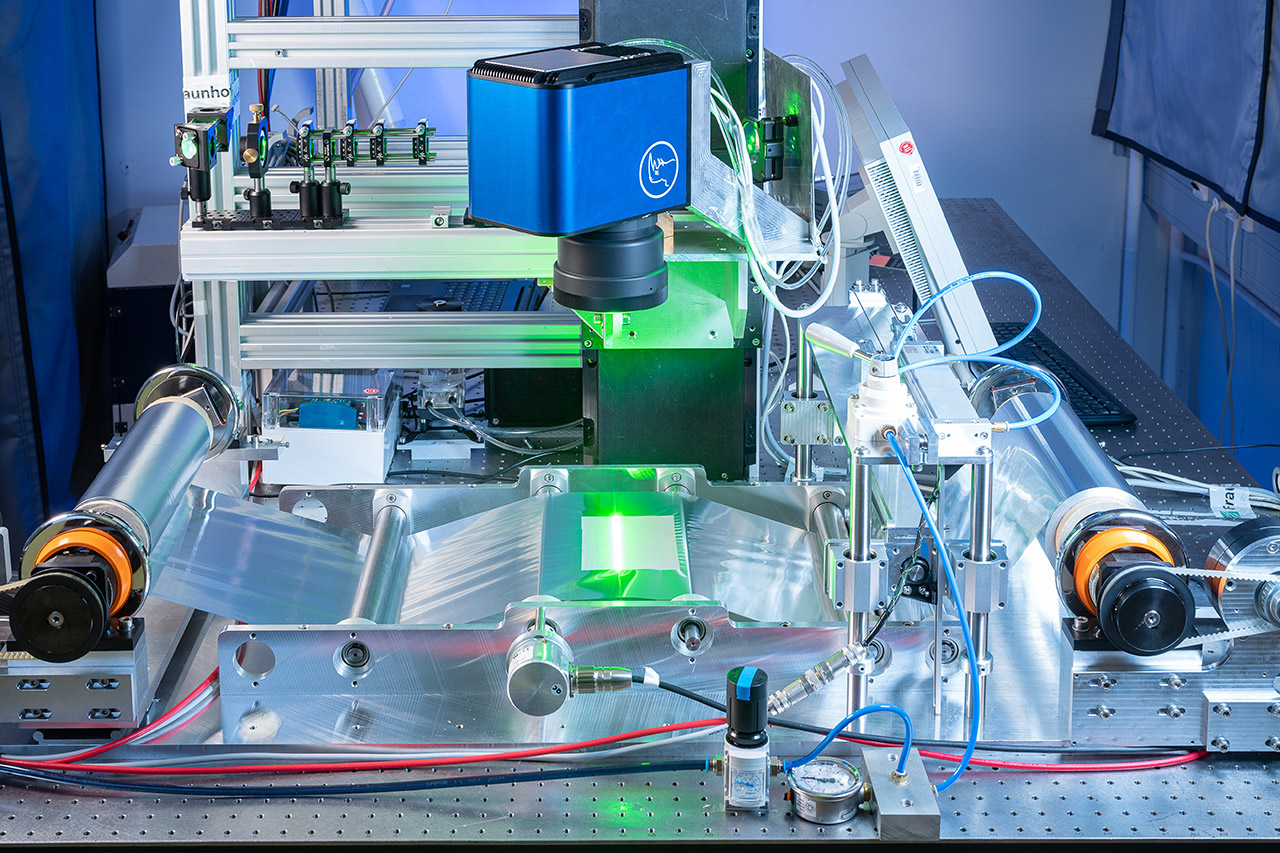
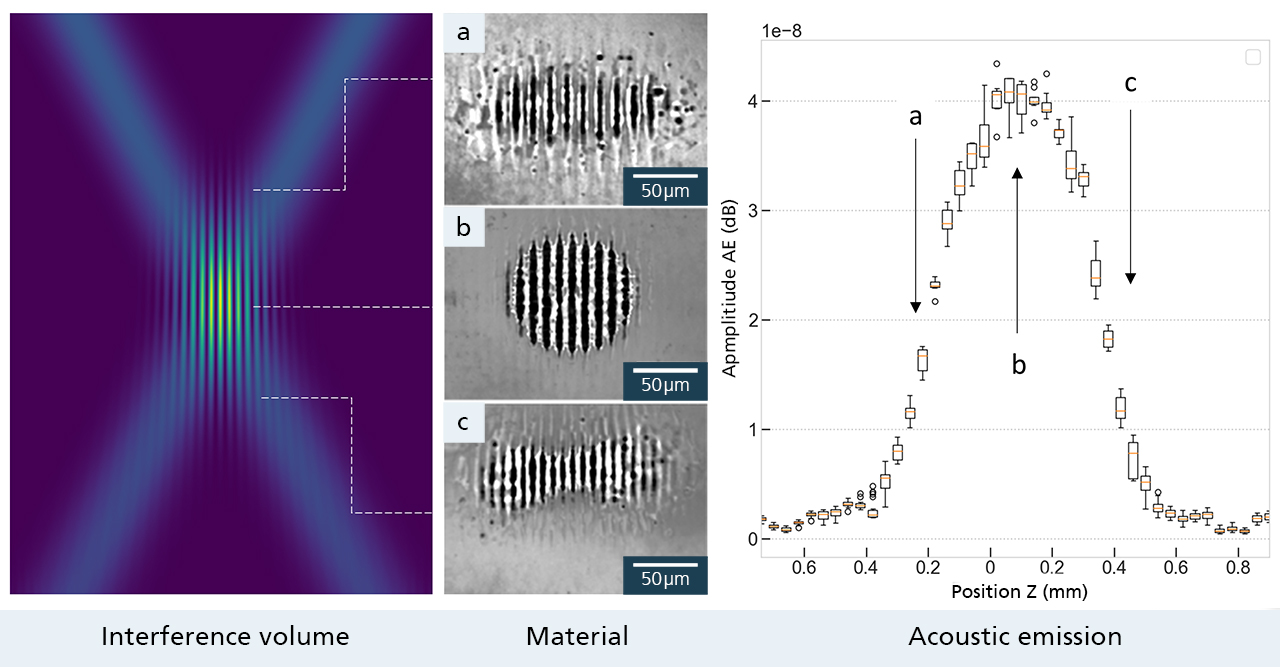
DLIP modules: DLIPscan, DLIPflex, …
The latest generation of DLIP processing heads allows to vary the structure period as well as orientation during processing. Thus, a wide range of surface structures can be realized with one system and process step.
On the one hand, the processing heads are offered individually and can be used e.g. in existing and robot-assisted laser systems. On the other hand, Fraunhofer IWS offers compact DLIP systems in which the head, the associated periphery (laser, housing, etc.) and a specially developed control software are already integrated.
DLIP roll-to-roll plant
Our goal is to keep the cost of an area to be processed as low as possible. Currently, we have achieved process rates of up to 0.9 square meters per minute at Fraunhofer IWS with laser processing. At the TU Dresden, with whom we are conducting joint research on the DLIP process, even 1.6 square meters per minute were possible by using polygon scanners. Even higher process rates are achieved with a roll-to-roll system. Here, it is not the film that is directly structured, but a stamp that forms the structure onto a film via a roll. Process rates of up to 10 square meters per minute can be achieved here.
Process monitoring (acoustic)
One strategy for process monitoring at DLIP, for example to treat complex and non-planar surfaces, is the detection and analysis of photoacoustic emissions. Over the last 35 years, it has been shown that the acoustic pressure generated by the impingement of a laser beam on a surface, leading to ablation, can be detected and analyzed with simple and commercially available transducers and microphones. Fraunhofer IWS characterizes the acoustic emissions during the production of linear microtextures with different spatial periods and depths, interprets the spectral signatures resulting from single point and interference ablation, and investigates the vertical extent of the interference effect based on the ablated area and its variation with interference period.
Prediction modeling of surface properties
As the performance of functional surfaces increases, the prediction of the resulting surface properties becomes increasingly important to reduce the development time for these functionalities. Consequently, advanced approaches to predicting the properties of laser-processed surfaces – known as predictive modeling – are needed. The findings from the analysis of photoacoustic emissions during the structuring process carried out at the institute enable the development of an autofocusing system that uses only the acoustic emission signals for 3D processing. This makes it possible to predict deviations in the DLIP processing parameters.