Tribological Coatings and Surfaces – Expertise in Friction Reduction and Wear Protection
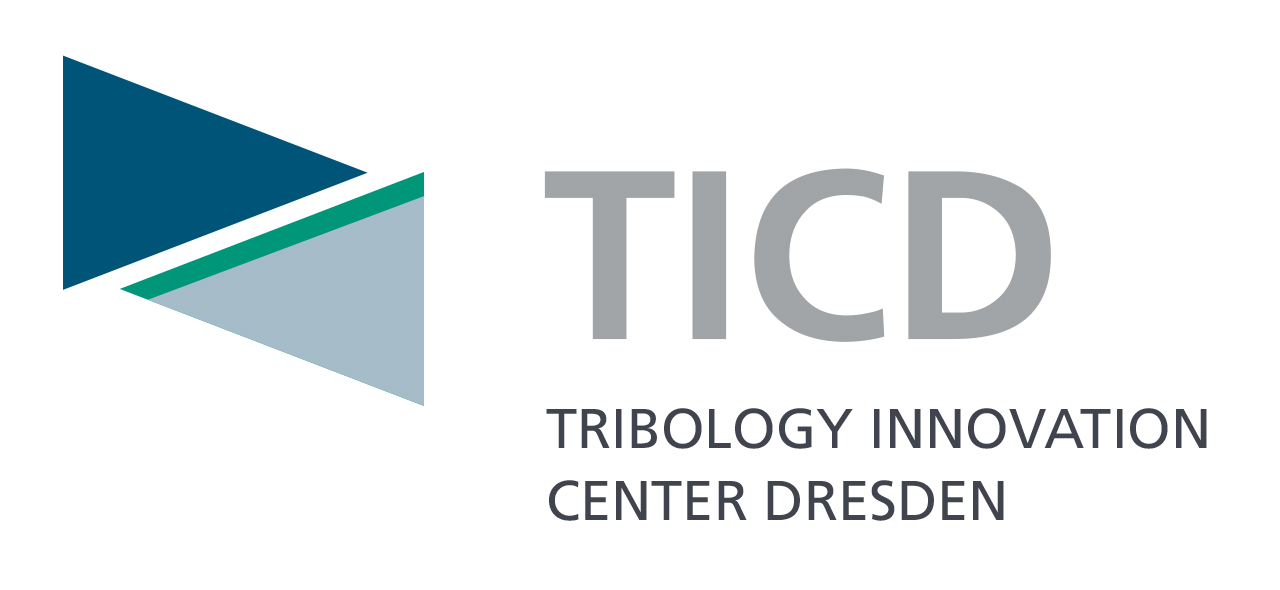
In times of global efforts to reduce climate-damaging CO2 emissions, the issue of friction often plays an underestimated role. After all, up to 20 percent of the primary energy used in a wide variety of vehicles, machines and systems is unnecessarily lost due to friction. In addition, there is the problem of tribological wear of tools and components, which limits the service life of systems in many applications or causes downtimes and maintenance times and results in high resource consumption.
In the Tribology Innovation Center Dresden (TICD) Fraunhofer IWS together with the TU Dresden researches tribological basic phenomena as well as suitable tribological measures, especially through coatings or other surface modifications. The goal is a significant reduction of friction and wear, whereby the solutions found should be as universally applicable as possible. Attention is paid to ensuring that the technologies developed are suitable for series production and can be used directly in the production of components and tools.