“UTILITAS” project develops ultra-light waste collection containers with HPCi® technology
Light vehicle superstructures thanks to optimized joints
The electrification of municipal vehicles is increasing the demand for ultra-light truck bodies to compensate additional battery weight. An adapted multi-material lightweight construction based on fiber-reinforced semi-finished plastic products and aluminum structures facilitates the cost-effective production of lightweight containers in small series. In this context, the type of joining technology plays a particularly important role.
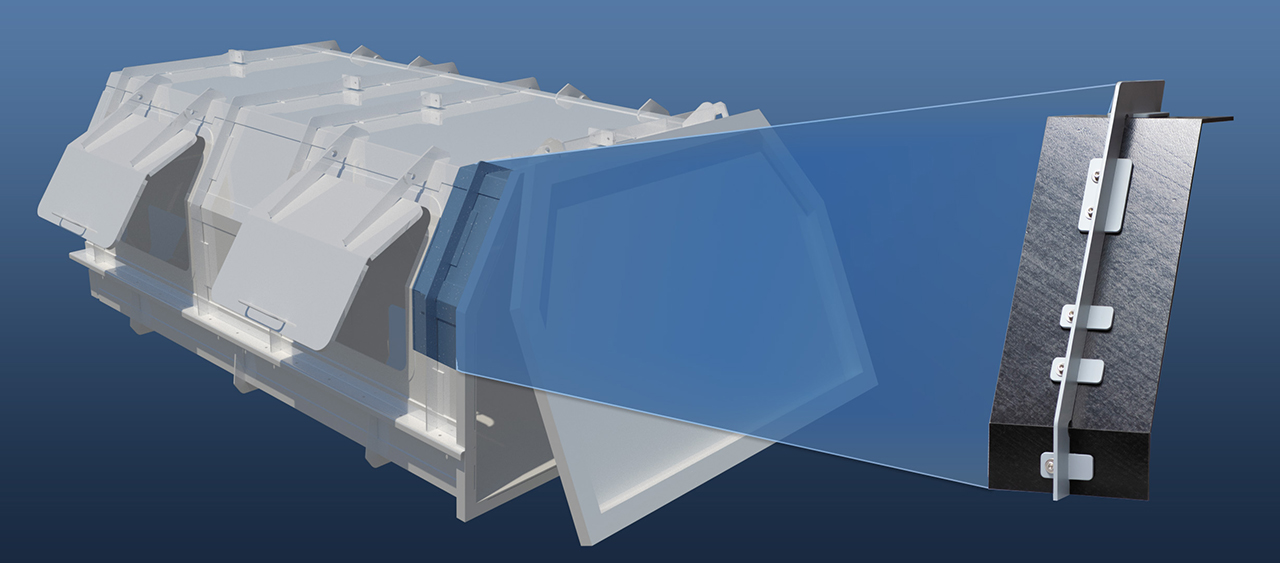
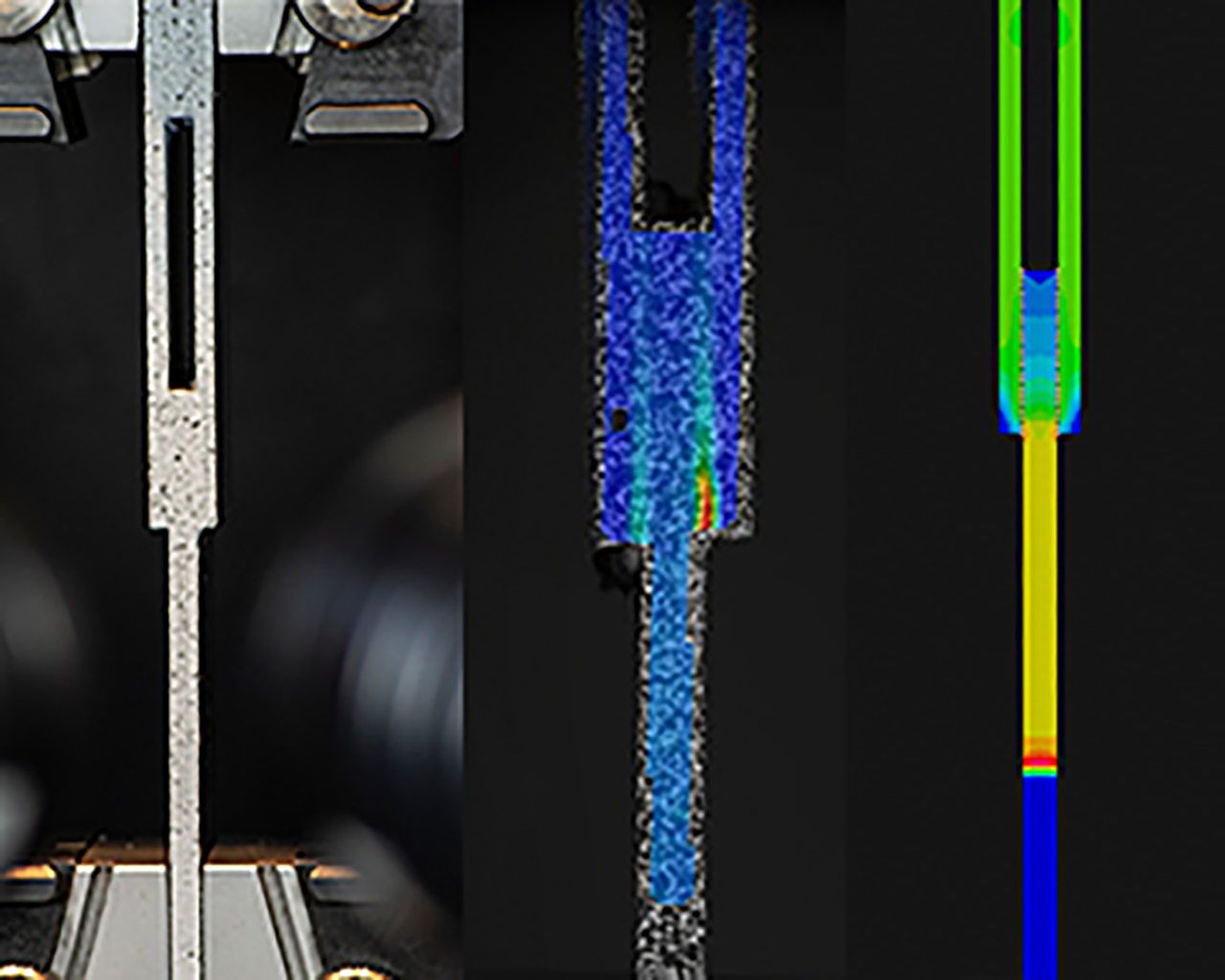
“The use of small commercial vehicles is increasing dramatically”, remarks Maurice Langer, engineer in the Fraunhofer IWS technology field Joining. “Their electrification protects the environment, but at the same time reduces maximum payloads”. To eliminate this disadvantage, the partners in the BMWi joint project “UTILITAS” are developing a waste collection container, which is both cost-effective to produce and ultra-light. In addition to the use of thermoplastic fiber-reinforced composites and aluminum, this container design is characterized in particular by load-suitable joining technologies. To join materials of different classes, screws or rivets as well as industrial adhesive joining can be used. If fiber-reinforced thermoplastics are to be joined with metal, the Fraunhofer IWS' HeatPressCool-integrative (HPCi®) technology can also be a promising solution. Maurice Langer describes the method as follows: “This process does not require any adhesives or fasteners, as the joining partners are locally pressed together. Simultaneous heating of the metal melts the plastic and bonds to the roughened metal surface.”
Joint design is the key factor
In order to implement container structures in multi-material design, it is essential to know the local loads, especially at the joints. Therefore, researchers at Fraunhofer IWS developed a simulation model to reproduce the behavior of solid joints under multiaxial loading conditions. “This enables us to spatially arrange and geometrically design the joint and thus to optimize it already during the design of complex multi-material constructions”, Langer concludes.