New joining method for the production of thermoplastic and thermoplastic-metal hybrid joints using reactive multilayer systems (RMS)
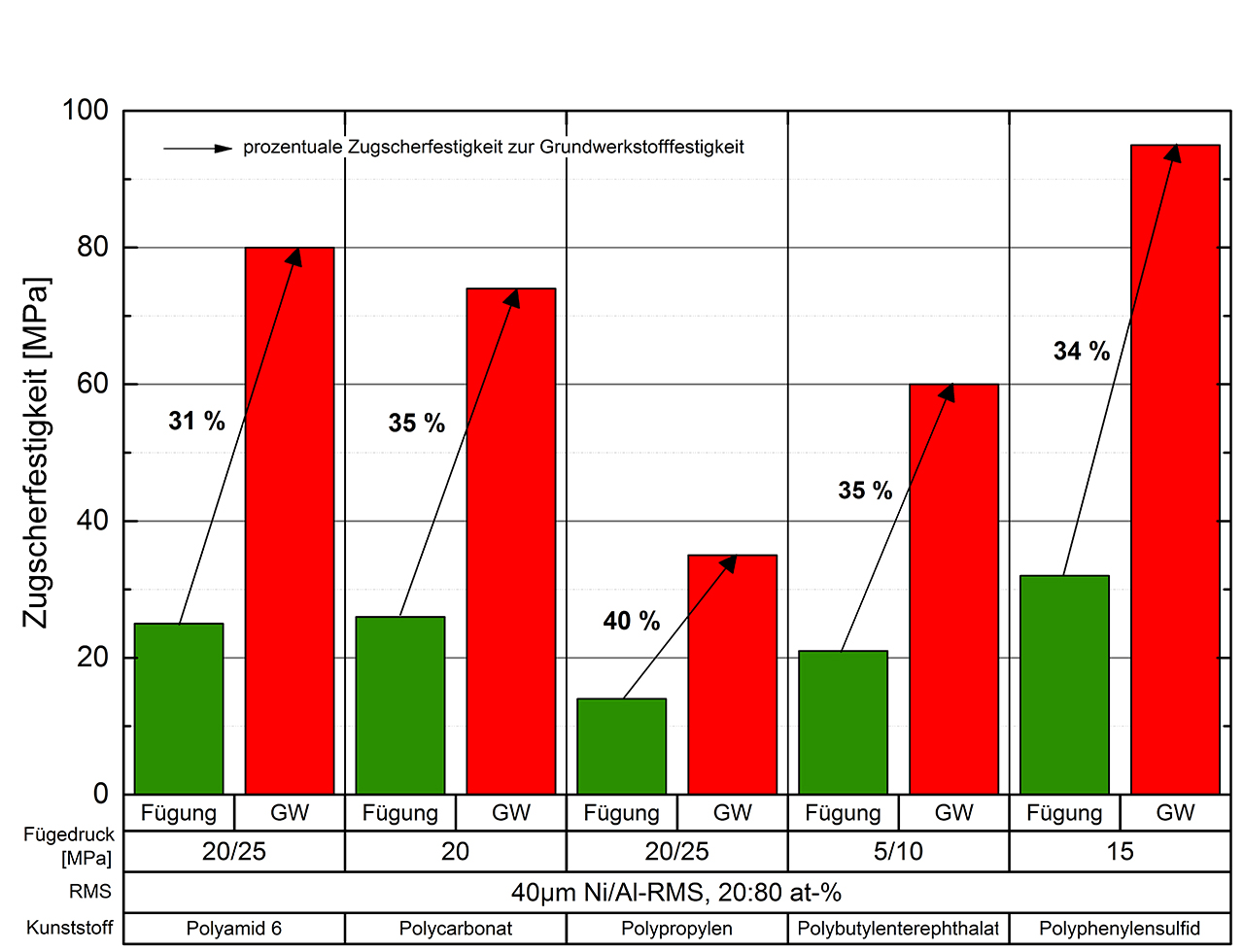
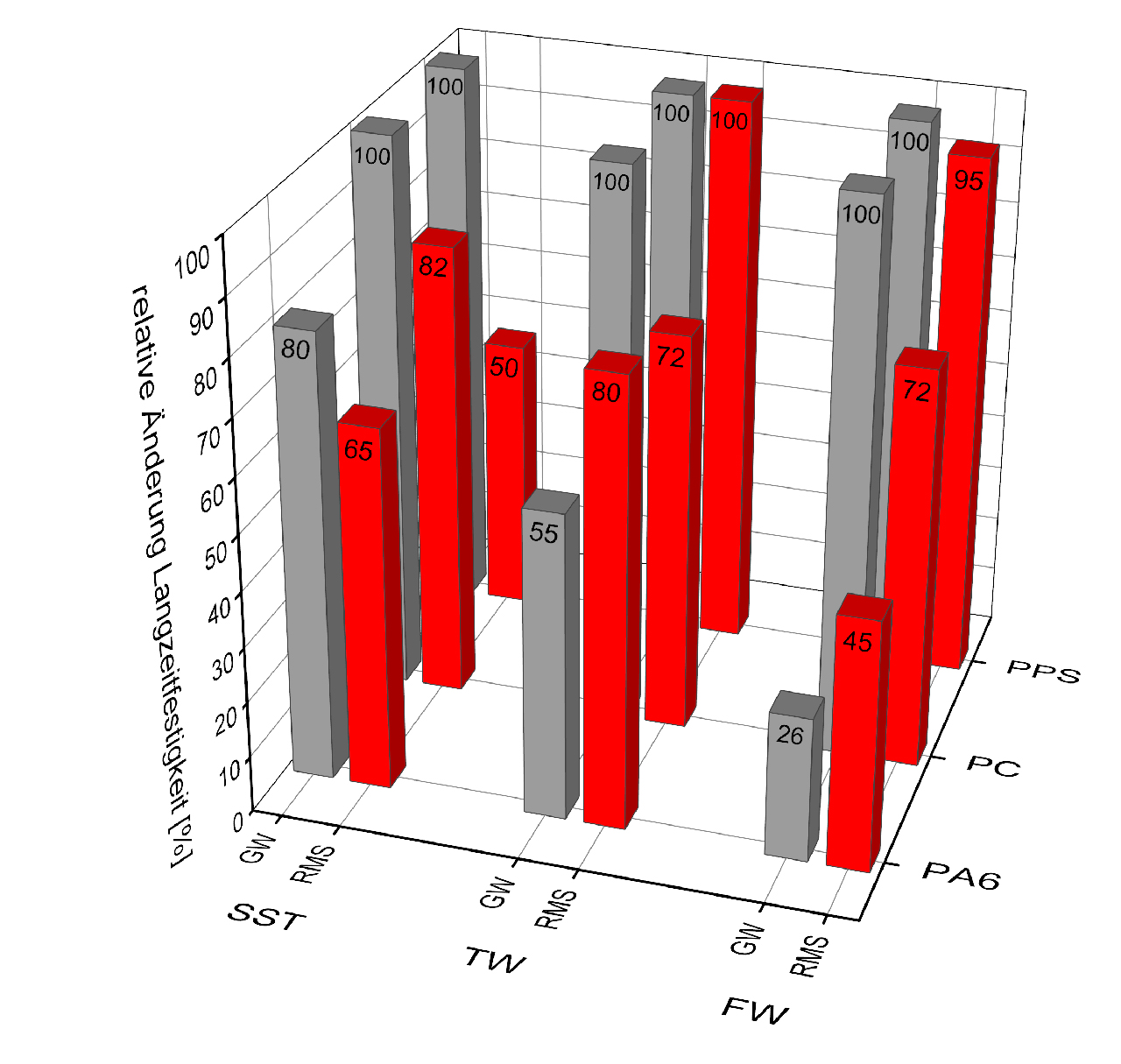

Motivation
In the course of the steadily increasing use of lightweight materials and construction methods, the demands on joining technologies are growing. In addition to lightweight metals and composites, great potential for weight savings is seen above all in the application of plastics. In this context, not only connections between plastics but also hybrid joints with materials from other classes have to be produced. In addition to the requirement for sufficiently strong joints, there are often other demands, such as the production of joints with long-term stability. Conventional joining processes such as soldering and welding usually generate a high heat input that can affect other areas of a component beyond the relevant joint. This can lead to undesirable property degradation. Joining with reactive multilayer systems (RMS) is a way of overcoming some or all of the limitations of conventional joining technologies.
Aims and approach
The aim of the AiF project is to develop the RMS joining technology for the field of thermoplastic materials and to realize strong and long-term stable joints without property degradation.
Within the scope of the research project, adapted low-energy Ni/Al RMS were developed and applied to five different thermoplastic materials. Various influencing factors, such as the energy content of the RMS and the joining pressure, were investigated and determined. Furthermore, the reactively joined plastic joints were analyzed with regard to joint type and mechanism, strength and long-term stability. The feasibility of hybrid joints of thermoplastics and metal was demonstrated in initial tests.
Innovations and perspectives
The use of reactive multilayer systems as a heat source for joining thermoplastics to each other and to metals allows the limitations of conventional joining methods to be overcome in whole or in part. Undesirable changes to the material structure are avoided and the joint strengths achieved are comparable to, and in some cases even higher than, those of commercially used joining processes. A particular advantage is that no costly pre- and post-treatment is required. In addition, RMS joints for thermoplastics achieve high long-term stability. Finally, the results were successfully transferred to functional samples in the context of housings.