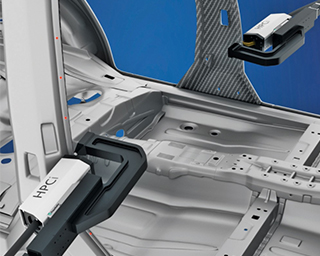
Weight reduction is one of the biggest challenges in automotive engineering: Lighter vehicles consume less fuel and help reduce CO2 emissions. With many years of expertise in researching materials, processes and technologies as well as systems engineering, we support automotive manufacturers and their suppliers in developing lightweight design concepts and processing advanced materials.
Body construction in particular benefits from material-optimized multi-material design: laser-based processes for joining and cutting as well as additive manufacturing technologies allow the realization of similar and hybrid lightweight designs using modern materials such as aluminum and fiber-reinforced plastic (FRP) composites. We also concentrate our research on safety-relevant topics such as airbag manufacturing and pollutant-free car interiors.