Contributions to Efficiency Enhancement in Arc PVD Coating of Turbo Engine Components (DigiParts)
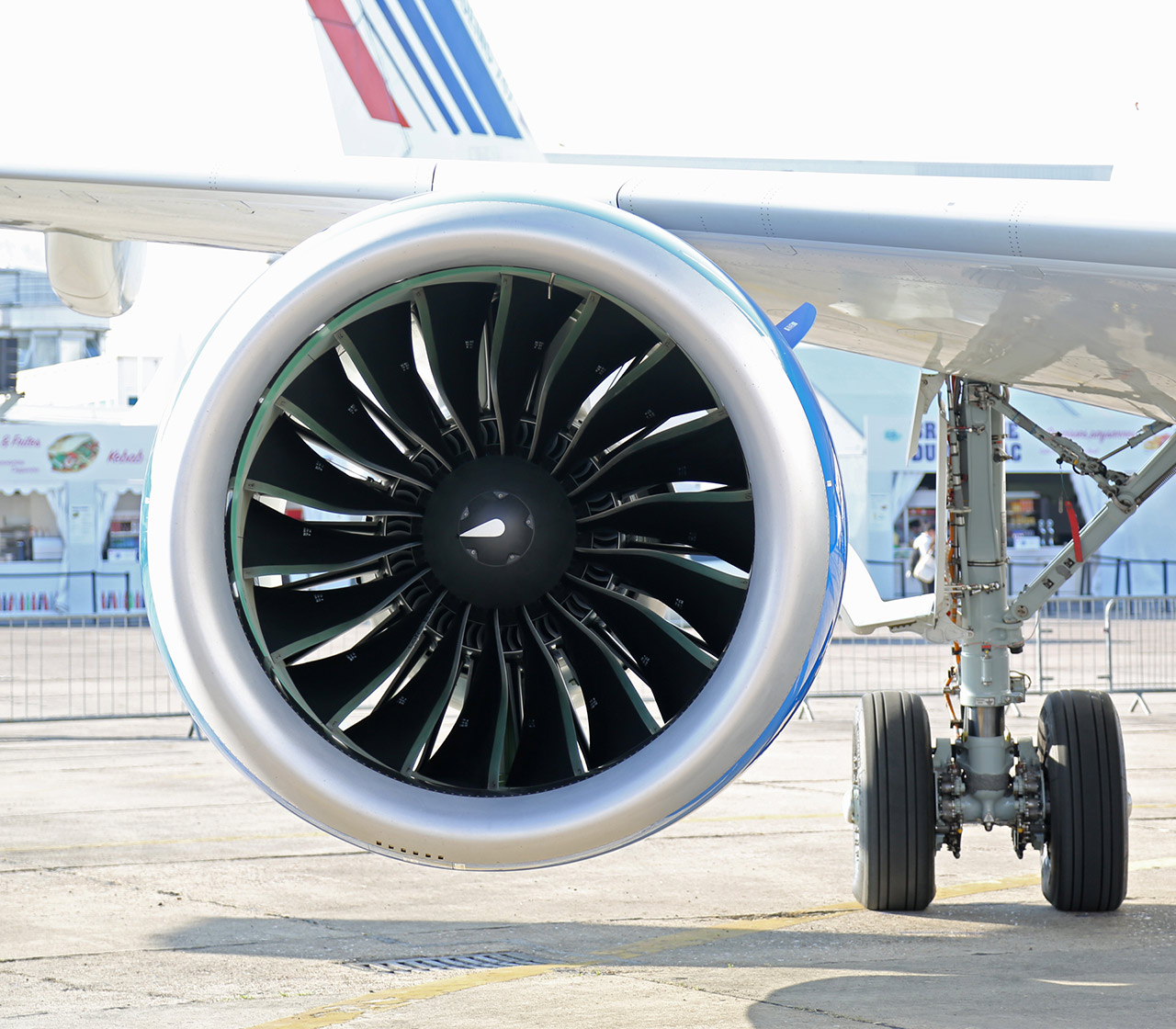
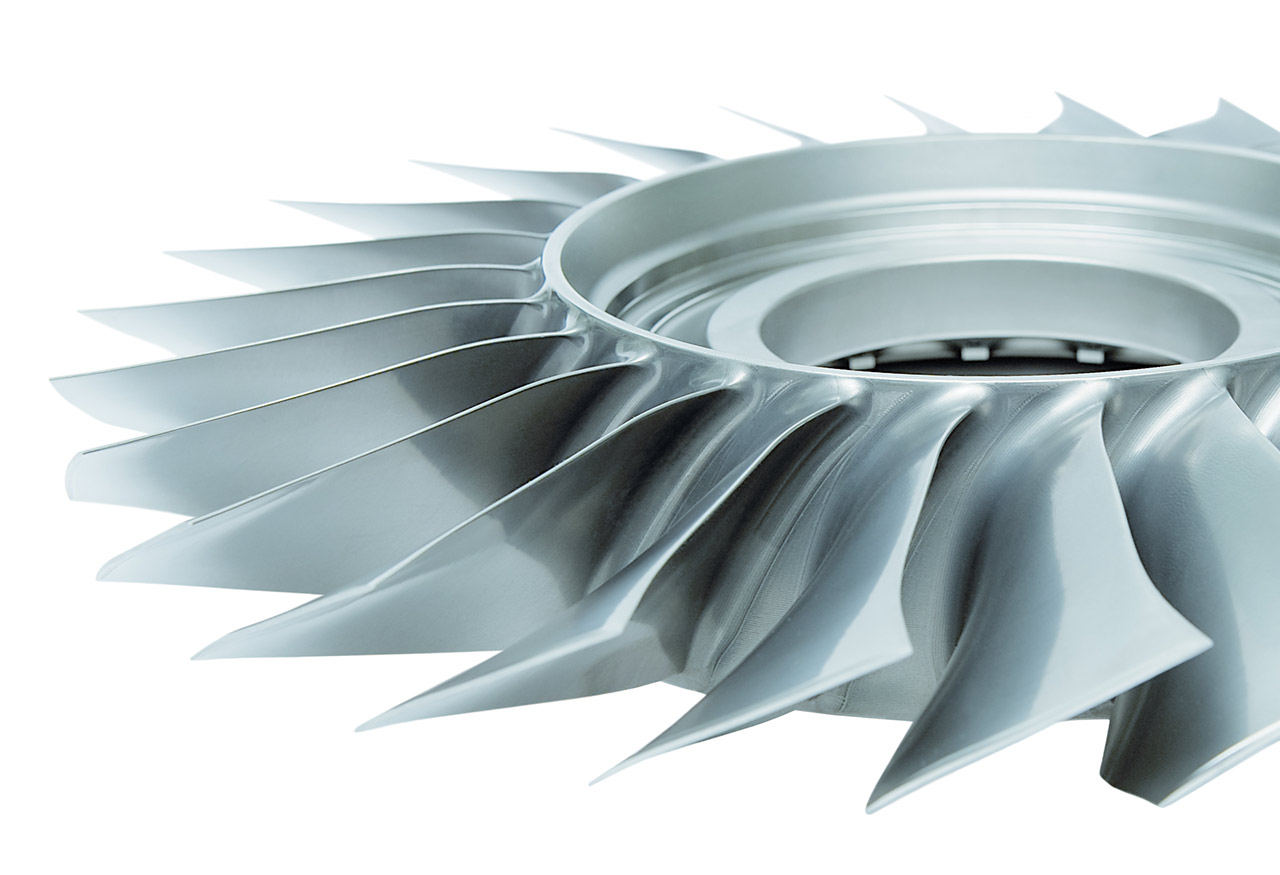

Motivation
MTU Aero Engines AG is a manufacturer of aircraft engines. Components subject to high stresses, such as compressor rotors, are routinely coated with wear-resistant coatings to meet current requirements for service value and service life. The coating is typically applied using the arc PVD process, with nitride hard materials being the primary coating systems used.
Project Aim
The aim of the project is to increase the efficiency of the arc PVD process used in order to create simulation tools that map important process properties and thus make them accessible for computer-aided optimization.
Procedure
The works are dedicated to three main topics. These are:
- Modeling of cathode processes: Computer models of relevant processes on the evaporator cathode of the arc process are created, evaluated with real process variables, and then used to optimize important process variables. The expected benefits are primarily improved utilization of the cathode material (less losses) and improved process stability.
- Modeling of plasma propagation and coating distribution: the propagation of the coating plasma from the source (arc evaporator) to the components to be coated and the resulting coating distribution are modeled. The models are evaluated with real processes. Finally, tools for future optimization of the arrangement of the components in the coating chamber, their movement as well as the process control are created.
In the long term, the implementation of the project is expected to result in considerable experimental effort reduction for setting up and optimizing new coating processes (e.g. for product changes) as well as an increase in production efficiency. In connection with this, a considerable saving of resources (material, energy) is intended.