Beiträge zur Effizienzsteigerung bei der Arc-PVD-Beschichtung von Triebwerkskomponenten (DigiParts)
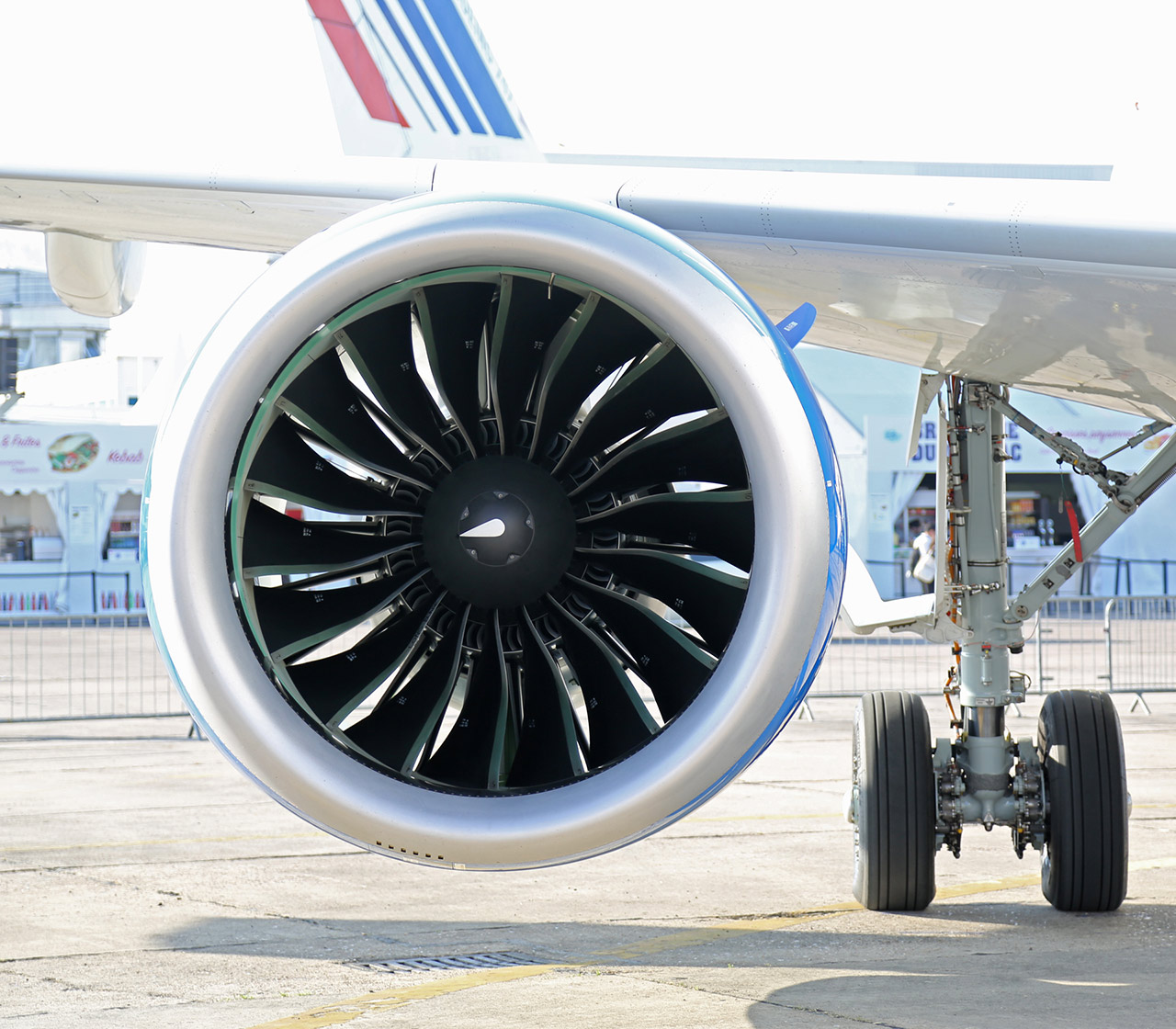
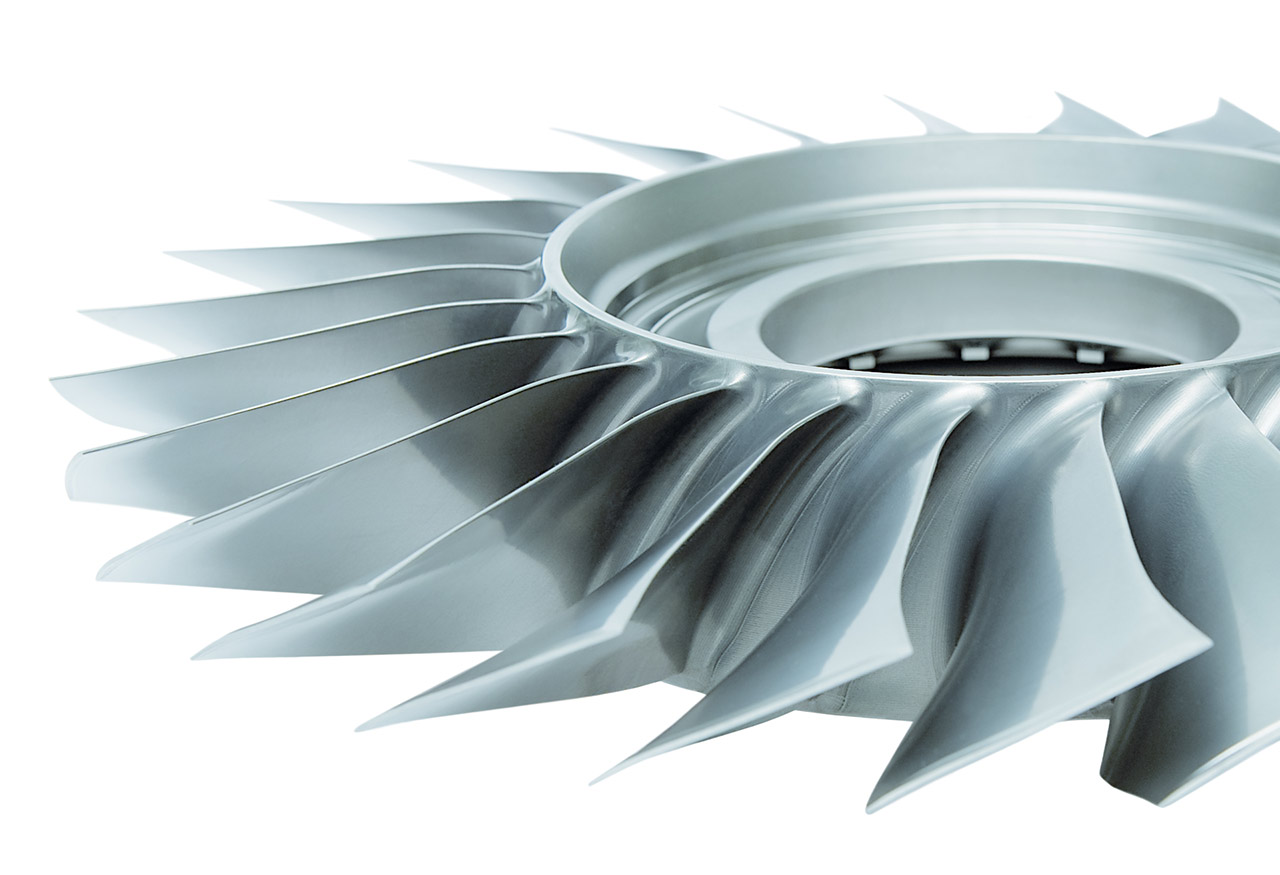
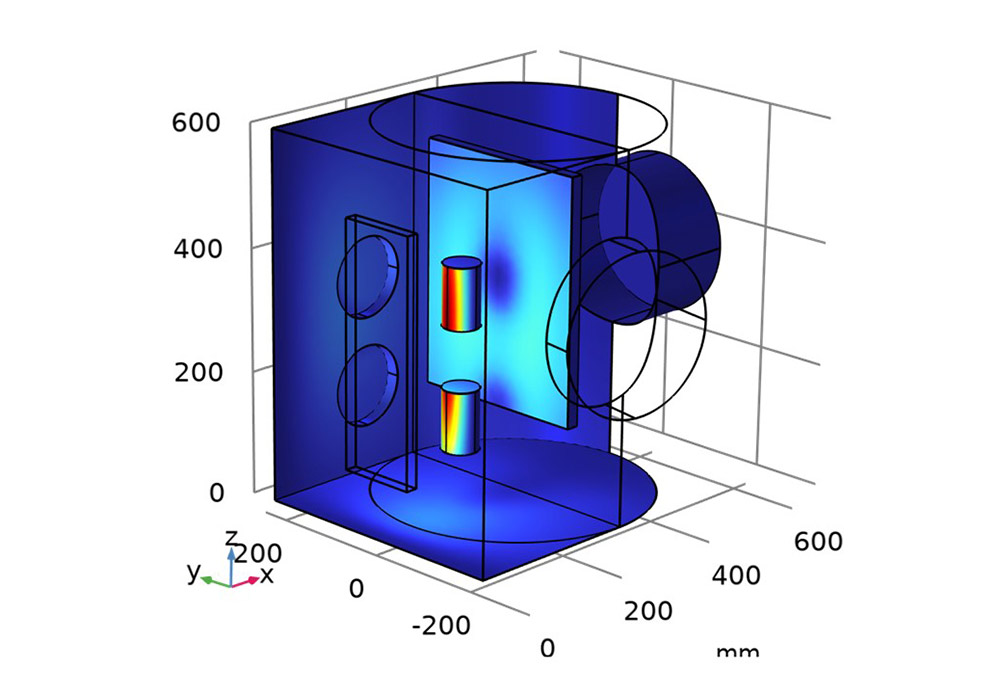
Motivation
Die MTU Aero Engines AG ist Hersteller von Triebwerken für Luftfahrzeuge. Stark belastete Komponenten, wie z. B. Verdichterrotoren, werden routinemäßig mit Verschleißschutzschichten versehen, um aktuelle Anforderungen an Gebrauchswert und Nutzungsdauer zu erfüllen. Die Beschichtung erfolgt typischerweise mit dem Arc-PVD-Verfahren, als Schichtsysteme werden vorrangig nitridische Hartstoffe appliziert.
Projektziel
Ziel des Vorhabens ist die Effizienzsteigerung des genutzten Arc-PVD-Prozesses durch Schaffung von Simulationswerkzeugen, die wichtige Prozesseigenschaften abbilden und dadurch einer rechnergestützten Optimierung zugänglich machen.
Vorgehen
Der Arbeiten sind drei Themenschwerpunkten gewidmet. Diese sind
- Modellierung von Kathodenprozessen: Computermodelle relevanter Prozesse auf des Verdampferkathode des Arc-Prozesses werden geschaffen, mit realen Prozessgrößen evaluiert und anschließend für die Optimierung wichtiger Prozessgrößen eingesetzt. Der erwartete Nutzen besteht vorrangig in einer verbesserten Ausnutzung des Kathodenmaterials (weniger Verluste) und verbesserter Prozessstabilität.
- Modellierung der Plasmaausbreitung und der Schichtverteilung: Die Ausbreitung des Beschichtungsplasmas von der Quelle (Arc-Verdampfer) zu den Komponenten, die beschichtet werden sollen, sowie die resultierende Schichtverteilung werden modelliert. Die Modelle werden mit realen Prozessen evaluiert. Schlussendlich werden damit Werkzeuge zur künftigen Optimierung der Anordnung der Komponenten in der Beschichtungskammer, deren Bewegung sowie der Prozessführung geschaffen.
Durch die Umsetzung des Vorhabens soll langfristig erheblicher experimenteller Aufwand zur Einrichtung und Optimierung neuer Beschichtungsprozesse (z. B. bei Produktwechsel) eingespart sowie eine Effizienzsteigerung der Produktion erreicht werden. Damit verbunden ist eine erhebliche Einsparung von Ressourcen (Material, Energie) beabsichtigt.