SNEAK PEEK: Erste Einblicke in den noch nicht veröffentlichten Jahresbericht 2020/2021
Bremsscheibenbeschichtung mit HICLAD®
Bremsscheiben rücken in der aktuellen Energiediskussion in den Fokus. Wissenschaftler des Fraunhofer IWS entwickeln mit HICLAD® ein Verfahrenskonzept, das den Korrosions- und Verschleißschutz per maßgeschneiderter Oberflächenfunktionalisierung maximieren soll. Im Blick steht dabei auch das Reduzieren von Feinstaubemissionen. Ein weiteres Plus: die kostengünstige Serienfertigung.
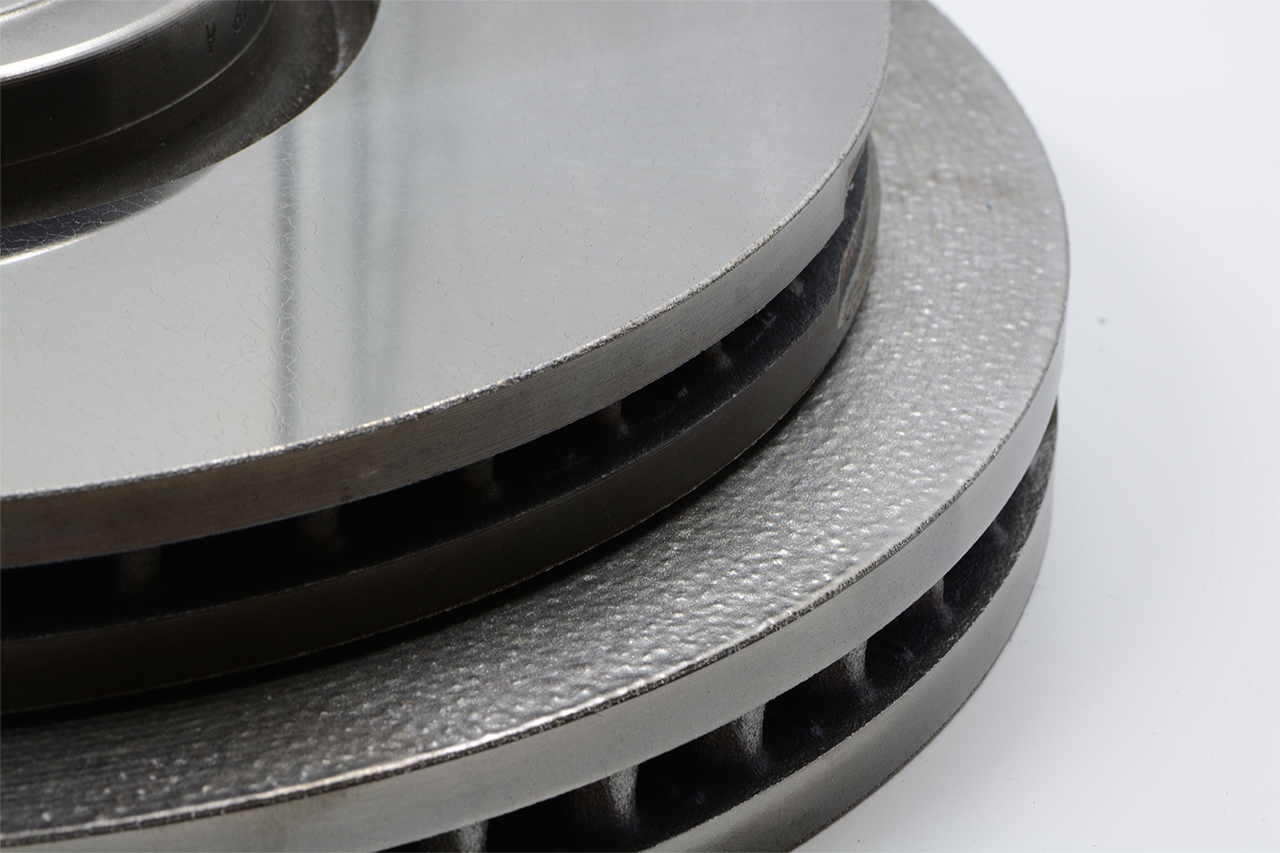

Das Laserpulverauftragschweißen gehört aufgrund seiner Schichteigenschaften und vielfältigen Werkstoffpalette zu den in der Industrie etablierten Beschichtungsverfahren zum Korrosions- und Verschleißschutz hochwertiger Bauteile. Für die Massenproduktion in großen Stückzahlen, wie z. B. von Bremsscheiben, erfüllt das konventionelle Laserauftragschweißen aber bislang lediglich bedingt die industriellen Kostenziele. Deshalb entwickelte das Fraunhofer IWS nun das Hochleistungs-Hochgeschwindigkeits-Laserauftragschweißen HICLAD®.
Kostengünstige Hochleistungsbeschichtung für optimale Bremseigenschaften und minimale Feinstaubemissionen
»Dieses neue Verfahren setzt speziell entwickelte Pulverdüsen und Optikkonfigurationen ein«, erklärt Holger Hillig, der sich mit der Thematik auseinandersetzt. Diese Vorgehensweise gestaltet so einen stabilen und reproduzierbaren Hochleistungsbeschichtungsprozess mit bis zu 20 Kilowatt Laserleistung. »Entsprechend steigen Produktivität und Auftragsleistung, die beide unabdingbar für eine Serienfertigung sind«, so der Ingenieur. Die Beschichtung der Bremsscheiben erfolgt in zwei Lagen: Einerseits entsteht eine etwa 125 Mikrometer dicke Korrosionsschutzschicht aus rostfreiem Edelstahl. Der HICLAD®-Prozess ist dabei so eingestellt, dass sich auf dem schwierig schweißbaren lamellaren Grauguss der Bremsscheibenrohlinge eine defektfreie Beschichtung ausbildet, die minimale Werte hinsichtlich Aufmischung, Spannungen und Verzug aufweist. Darauf wird die Schweißlage mit der eigentlichen tribologischen Funktion aufgetragen. Sie erhält ihre Verschleißfestigkeit durch Hartstoffe wie Wolframkarbid, Titankarbid oder Chromkarbid, die in einer Eisen-Basislegierung eingelagert werden. Das Schichtsystem und die Mischungsverhältnisse sind so eingestellt, dass sich in Kombination mit den Bremsbelägen eine optimale Reibpaarung hinsichtlich der Bremseigenschaften und minimaler Feinstaubemissionen erzielen lässt.
Der Prozess ist dank Prozessregelung und Schmelzbadüberwachung äußerst robust, sodass sich z. B. auch preiswerte Pulver mit breiterer Korngrößenverteilung verwenden lassen. »Dadurch sinken die Werkstoffgesamtkosten erheblich«, sagt Hillig. Die Qualität des Schichtsystems lässt sich zerstörungsfrei mittels LAwave®-Technologie kontrollieren. Die vorgestellte Beschichtungslösung reduziert die Feinstaubemission beim Bremsen deutlich und vermeidet Korrosionsschäden, die üblicherweise bei unregelmäßiger Nutzung entstehen – wie etwa in elektrischen Fahrzeugen. Die Lebensdauer der behandelten Bremsscheiben verlängert sich erheblich.