Thermoplastischer Rumpf
Im Projekt TRumpf wurden neuartige Fertigungs- und Verarbeitungstechnologien für Flugzeugrumpfstrukturen auf Basis kohlenstofffaserverstärkter Hochleistungsthermoplaste entwickelt.
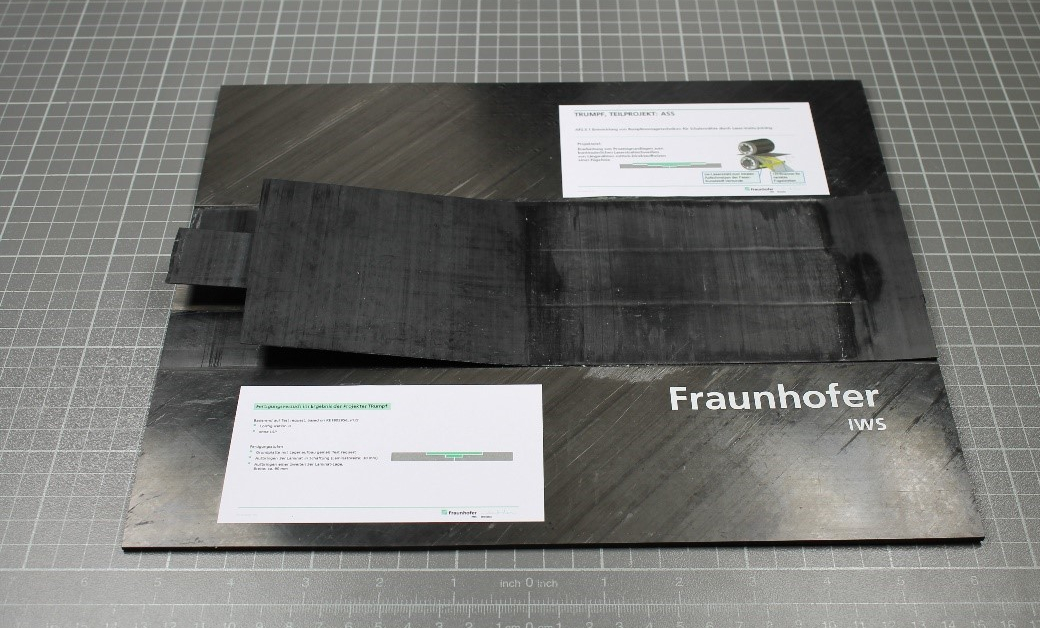
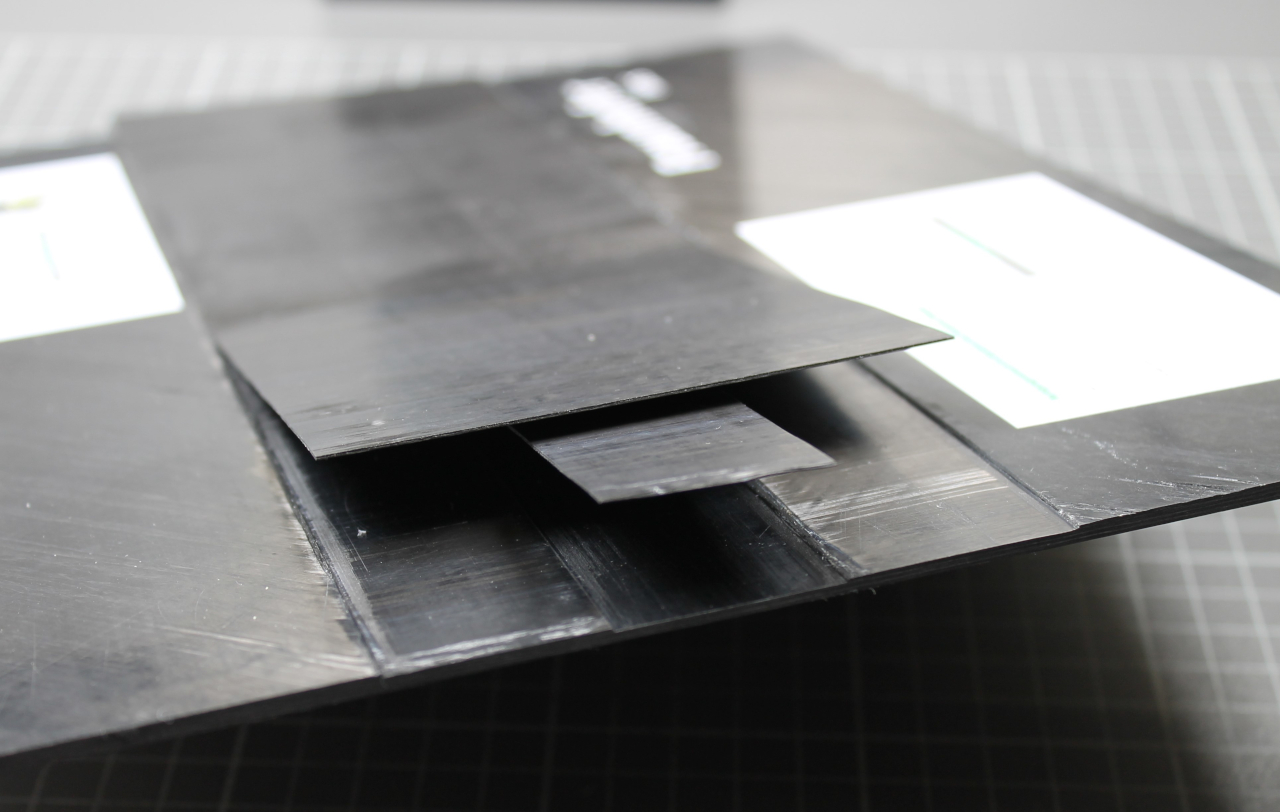
Motivation
Die Forschung der letzten Jahre hat zu Erkenntnissen geführt, die die Verwendung der Thermoplasttechnologien für den Bau von Strukturen für Zivilflugzeuge, insbesondere für Rumpfstrukturen, als vorteilhaft erscheinen lassen. Werkstoffe auf Basis thermoplastischer Polymere bieten aufgrund ihrer Wiederaufschmelzbarkeit vielfältige Vorteile hinsichtlich ihrer Verarbeitbarkeit im Vergleich zu den gängigen duroplastischen Materialien.
Ziele und Vorgehen
Im Rahmen des Projekts TRumpf wurden Technologien auf die Eignung zur Herstellung von Rumpfstrukturen geprüft und validiert und anschließend deren wirtschaftliche und technologische Vorteilhaftigkeit in einem holistischen Ansatz analysiert werden. Das Fraunhofer IWS entwickelte im zugehörigen Teilvorhaben TRumpf-ASS (Automatisierte Oberflächen-Schutz- und Schweiß-Prozesse für PEKK-Rumpf) mit dem »Laser-in-situ-Joining« eine Fügetechnologie, welche das kontinuierliche Laserschweißen (konsolidieren) von kohlenstofffaserverstärkten Thermoplastlaminaten zur Erzeugung von Rumpf-Längsnähten ermöglicht.
Das Verfahren lehnt sich dabei an bereits erprobte automatisierte Ablegeprozesse wie das Automated Tape Laying (ATL) an – jedoch mit einem entscheidenden Unterschied: Mit der neu entwickelten Technologie können vorkonsolidierte und mehrlagige multidirektional verstärkte Halbzeuge in einem einzigen Prozessschritt aufgebracht werden. Gegenwärtige Fertigungsprozesse sind hierbei auf einlagige unidirektional verstärkte Bänder (sog. Tapes) beschränkt. Durch die Möglichkeit, Halbzeuge nun auch quer zu den implementierten Faserrichtungen ablegen zu können, ergeben sich neue fertigungstechnische Chancen für die Fügung komplexer Strukturen.
Innovationen und Perspektiven
Die im Vorhaben erarbeitete Technologie ebnet den Weg für neue Fertigungsmöglichkeiten für thermoplastische Flugzeugrumpfstrukturen, welche die Anzahl der zusätzlich benötigten Verbindungselemente in kommenden Flugzeuggenerationen drastisch reduzieren könnte. Diese Ersparnis würde sich im resultierenden Gesamtgewicht und damit direkt in Form einer Emissionsreduktion darstellen.