Sichere Bauteilentwicklung durch anwendungsnahe Absicherung im Labor
Prüfen jenseits der Normung
Normgerechte Kennwerte sind die unverzichtbare Basis für die Werkstoffauswahl zu Beginn einer Bauteilentwicklung. Mit fortschreitendem Entwicklungsstadium eines neuen Produkts treten jedoch anwendungsorientierte Belastungsszenarien in den Fokus, die sich am Fraunhofer IWS durch eine unmittelbare Verknüpfung zwischen Prozesswissen und werkstofflichem Verständnis in individuelle Prüfszenarien umwandeln lassen.
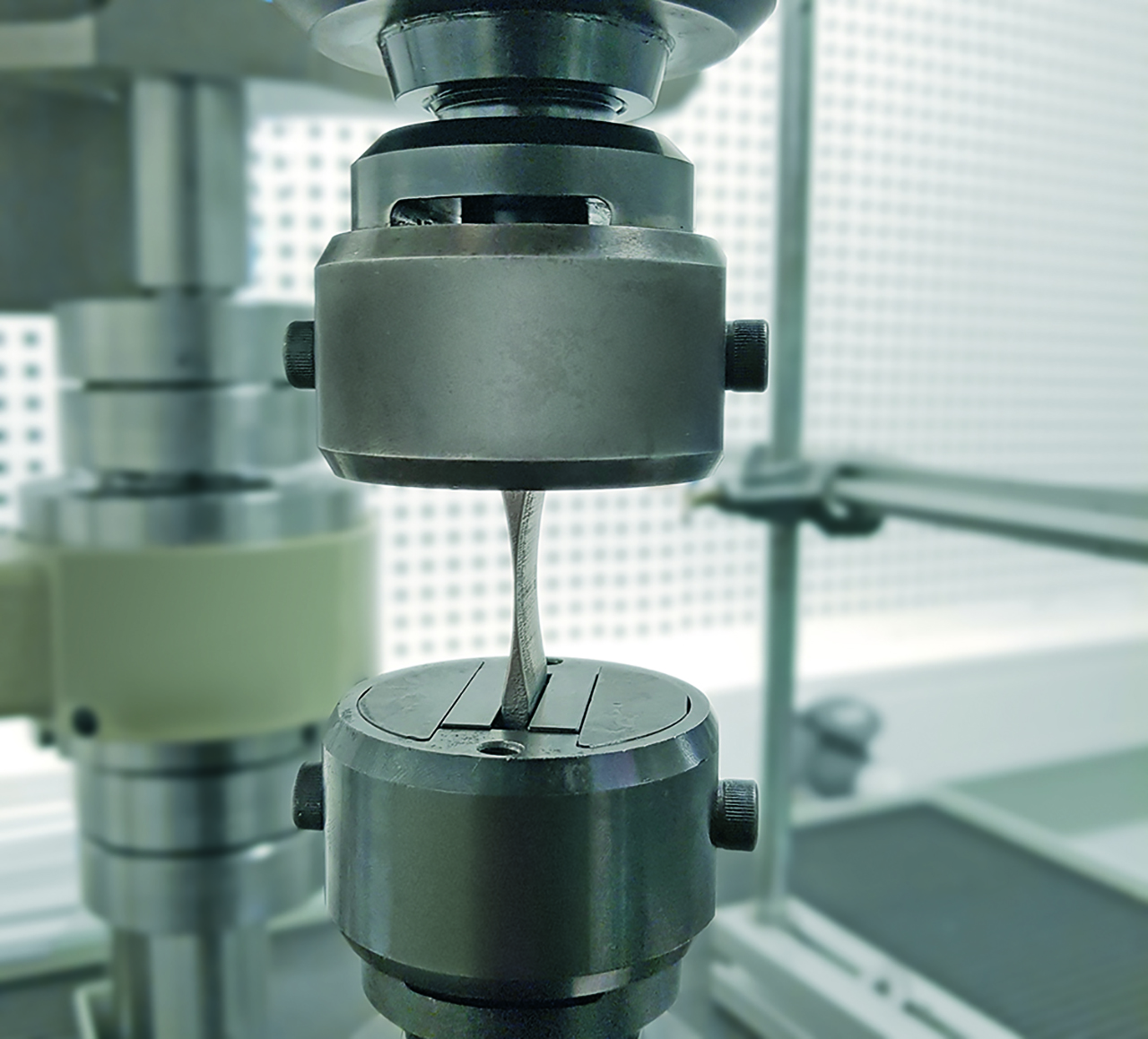

Die moderne Bauteilentwicklung verknüpft sowohl virtuelle als auch experimentelle Methoden der beanspruchungsgerechten Absicherung. In den frühen Entwicklungsphasen werden Bauteileigenschaften vorwiegend auf der Basis standardisierter Werkstoffeigenschaften simuliert. Deren experimentelle Bestimmung erfolgt am Fraunhofer IWS mittels normgerechter Prüfungen, wie des Zugversuchs nach DIN EN ISO 6892 oder der Wöhlerlinienermittlung nach DIN 50100. In den abschließenden Stadien der Bauteilentwicklung verschieben sich die Anforderungen an die experimentelle Prüfung. Dann liegt der Schwerpunkt auf der Übertragbarkeit von Prüfergebnissen auf den konkreten Einsatzfall. »Bei der experimentellen Absicherung von Komponenten legen wir den Fokus auf die spezifische Belastungssituation der späteren Anwendung und bilden diese möglichst realitätsgetreu nach«, führt Robert Kühne aus, der am Fraunhofer IWS die Gruppe Werkstoff- und Bauteilzuverlässigkeit leitet. »In aktuellen Untersuchungen entwickelten wir beispielsweise eine angepasste Ermüdungsprobengeometrie, die den besonderen Randbedingungen der additiven Fertigung dünnwandiger Strukturen gerecht wird.« Die bauteilnahe Form ermöglicht den Vergleich spezifischer Oberflächenzustände bei einer bauteilähnlichen Geometrie und prozesssicheren Herstellung.
Kontaktermüdung von Schichtsystemen
Ein weiteres Forschungsthema ist die qualitative Bewertung der Festigkeits- und Verschleißeigenschaften hochfester Schichtsysteme auf der Basis von amorphem Kohlenstoff (ta-C). Mithilfe einer angepassten Prüfmethodik gelang es den Wissenschaftlern, die Widerstandsfähigkeit von unterschiedlichen Schichtsystemen gegenüber wiederkehrenden äußeren »Mini-Impacts« zu bewerten. »Die Ermüdung der Beschichtung wird durch einen wiederholten Kontakt zwischen einem sphärischen ›Indenter‹ und der Prüfoberfläche hervorgerufen. Neben der reproduzierbaren Belastung spielt die begleitende metallografische und elektronenmikroskopische Schädigungscharakterisierung eine entscheidende Rolle«, erklärt Kühne. Umgebungseinflüsse, wie beispielsweise hohe Einsatztemperaturen, werden bei der finalen Bauteilerprobung ebenfalls berücksichtigt, da sie das Eigenschaftsprofil erheblich beeinflussen können. Am Fraunhofer IWS ist die Ermüdungsprüfung von Bauteilen bis zu einer Temperatur von 900 °C möglich. Aktuell prüfen Wissenschaftler auch laserstrahlgeschweißte Bauteile aus dem Abgasstrang von Fahrzeugen in diesem Temperaturbereich, um die Übertragbarkeit der Ergebnisse in die Praxis sicherzustellen.