Hermetisches Fügen von MEMS-basierten Bauelementen mithilfe von reaktiven Multischichtsystemen (RMS)
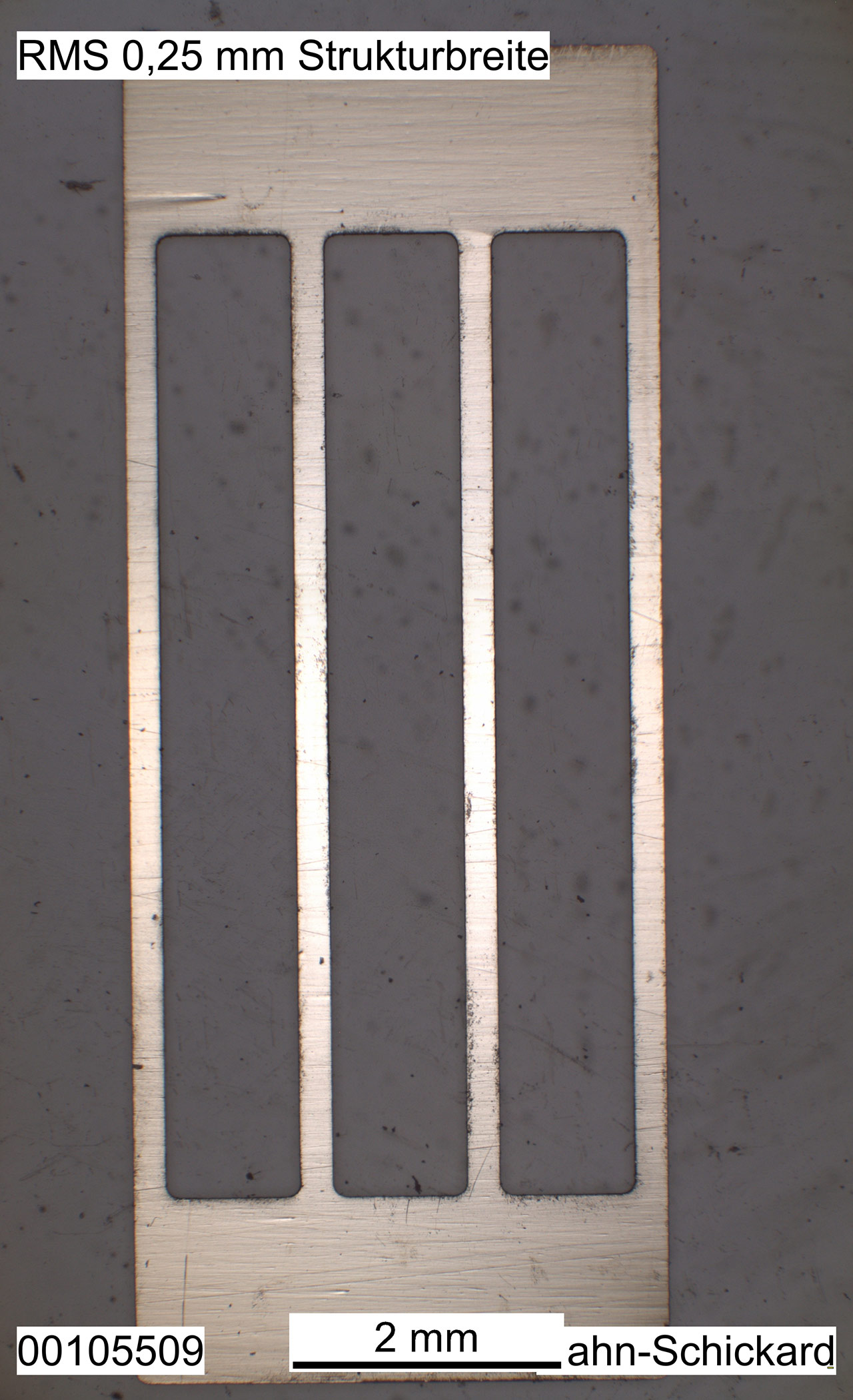
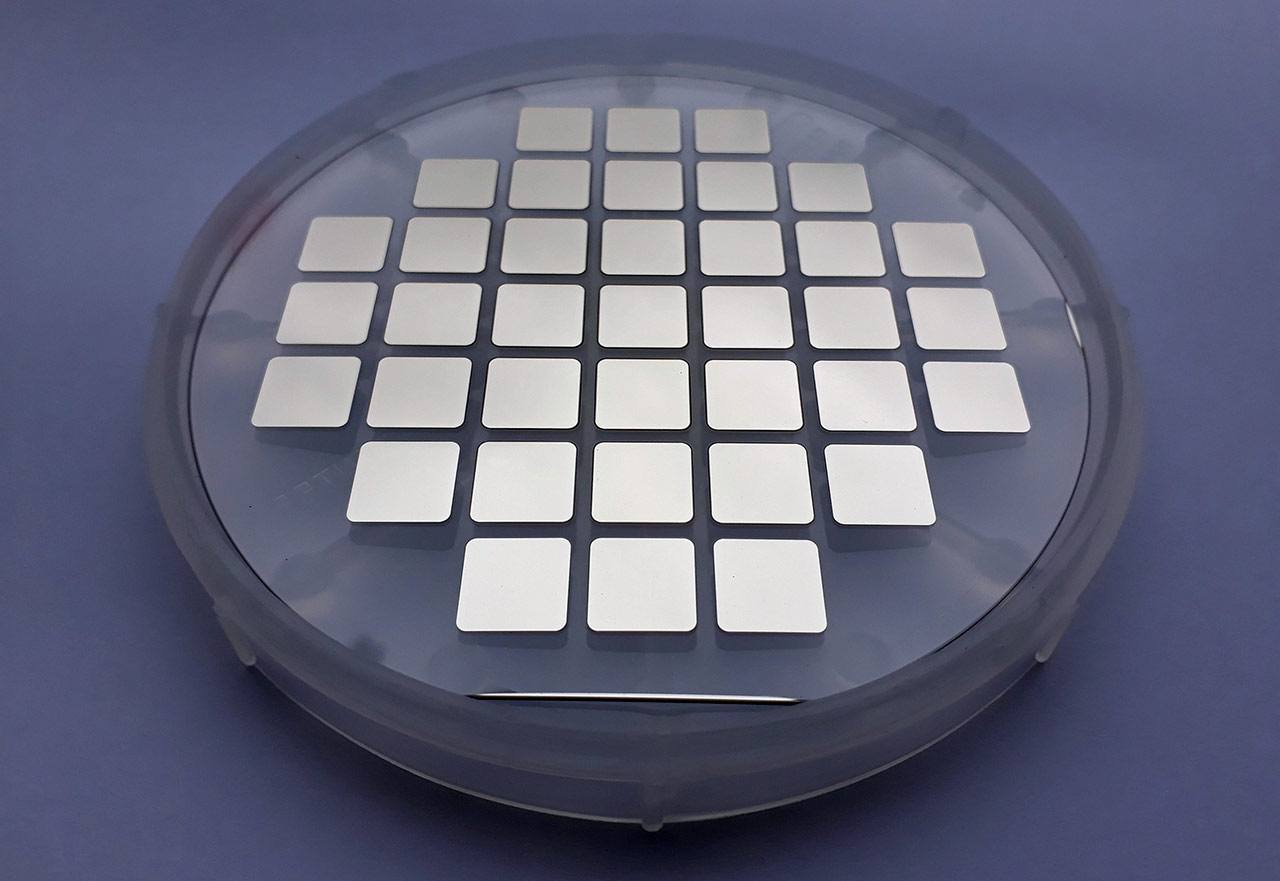
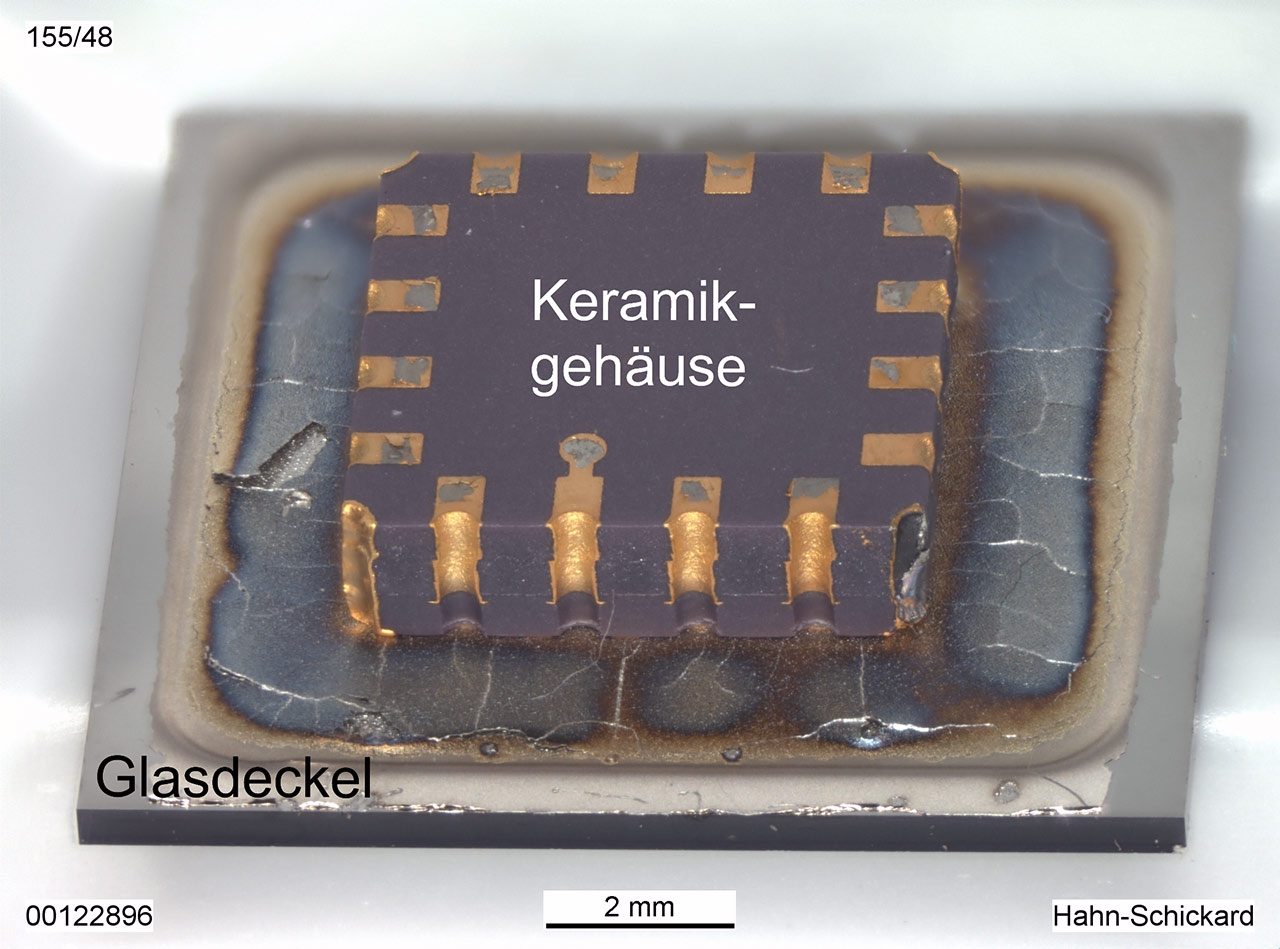
Motivation
Fügeprozesse müssen in der Mikrosystemtechnik neben einer dauerhaften Verbindung zwischen Komponenten einer Baugruppe meist noch zusätzliche Funktionen abdecken, wie z. B. hermetische Dichtheit. Bei den derzeit eingesetzten Fügeverfahren herrschen zum Teil hohe Prozesstemperaturen, die beim Einsatz verschiedener Materialien mit unterschiedlichen Wärmeausdehnungskoeffizienten zu thermomechanischem Stress in der Fügezone führen. Dieser kann vermieden werden, wenn die zum Fügeprozess erforderlichen Temperaturen nur auf die Fügestelle begrenzt wirken, die Bauteile selbst aber davor verschont bleiben. Dies ist aufgrund der Anpassbarkeit der reaktiven Multischichtsysteme (RMS) möglich.
Ziele und Vorgehen
Das Ziel des Forschungsvorhabens bestand darin, das Fügen mittels reaktiver Multischichtsysteme (RMS) für die Mikrosystemtechnik zu entwickeln. Folgende Fragestellungen wurden schwerpunktmäßig behandelt: Voraussetzungen für die Herstellung von Verbindungen mit hermetischer Feinleckdichtheit sowie grundsätzliche Parameter und Bedingungen beim RMS-Fügen.
Im Rahmen dieses Forschungsprojekts wurden sowohl rissarme Ni/Al-RMS, als auch hochenergetische Zr/Si-RMS entwickelt und zur Erzielung hermetisch dichter Verbindungen genutzt. Das Zr/Si-System bietet dabei mehrere Vorteile. So kann im Vergleich zum Ni/Al-System die doppelte Energie freigesetzt werden, wodurch die für das Fügen notwendigen Schichtdicken auf wenige Mikrometer reduziert werden. Gleichzeitig besitzt diese RMS eine geringere Schwindung, was zu einer Minimierung der Rissbildung führt. Für Fügeversuche mit Testsubstraten wurden Zr/Si-RMS sowohl als freistehende, optional vorbelotete Folien, als auch in Form integrierter, direkt auf Bauteil- und Waferlevel abgeschiedener Schichtsysteme hergestellt.
Innovationen und Perspektiven
Im Ergebnis des Forschungsvorhabens konnte gezeigt werden, dass für Verbindungen in der Mikrosystemtechnik durch die Anpassung des RMS-Typs, deren Eigenschaften hinsichtlich freiwerdender Energiemenge und Reaktionstemperatur und der Fügeprozesstechnik schädigungsarme und hermetisch dichte Verbindungen geschaffen werden können. An einem Funktionsmuster der Fa. First Sensor Microelectronic Packaging wurde die RMS-Fügetechnolgie umgesetzt. Dabei haben die Faktoren Oberflächenebenheit, RMS-Typ, Belotung und Fügedruck entscheidenden Einfluss auf die Verbindungseigenschaften. Es traten keine Risse im Glas auf und es wurden Leckraten von 2•10-8 mbar•l/sec gemessen.