High-rate joining of bipolar plates from two half plates (HP2BPP)
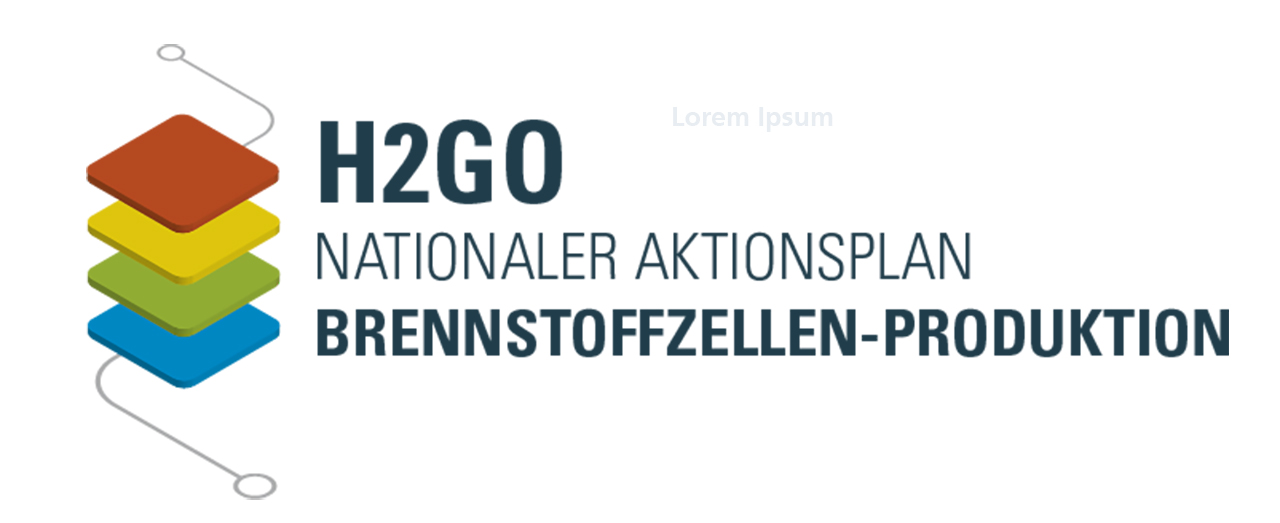

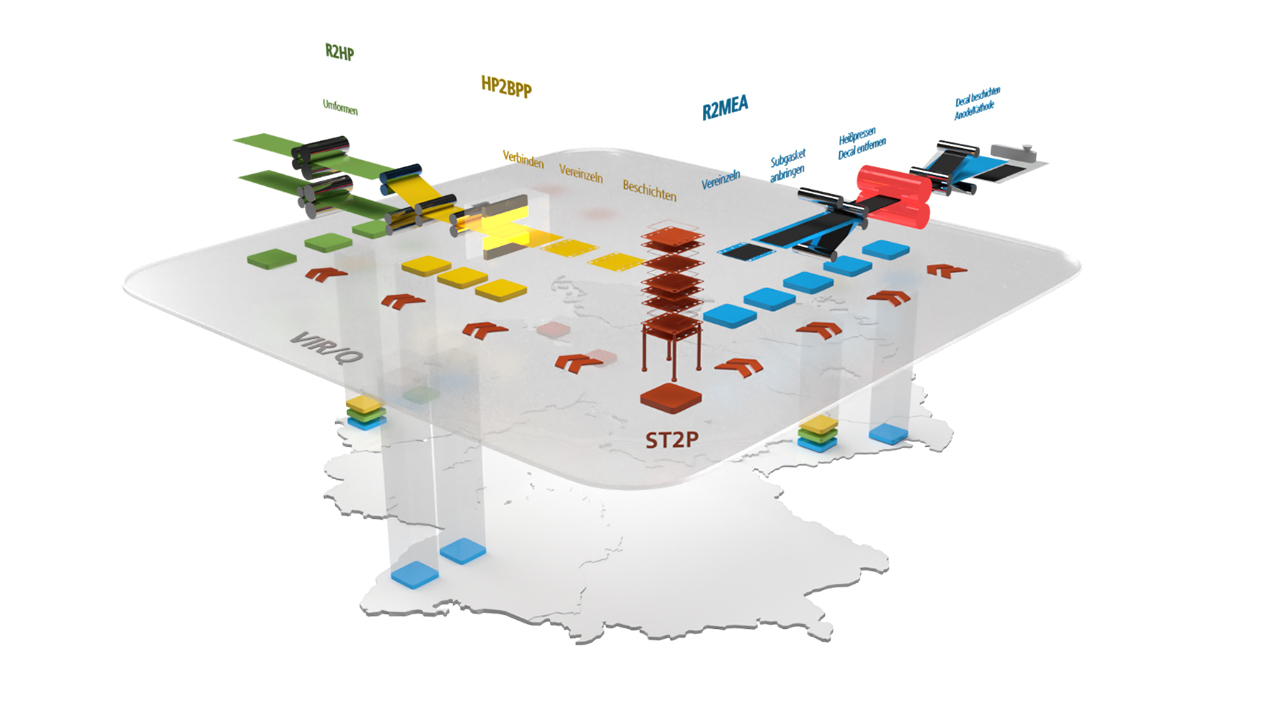
Project Description
Within the H2GO cluster, the HP2BPP joint project is developing the technologies and equipment that will be needed in the future for the high-rate and simultaneously flexible production of bipolar plates (BPP) for fuel cells.
Based on the holistic continuous process idea, the half-plates produced by the R2HP compound are fed into the joining process. For this purpose, the necessary developments are being driven forward to enable the required production rates to be met in terms of quality during thermal joining, joining by bonding, surface coating, separating, activating, cleaning and the evaluation/testing of the bipolar plate component.
The research focus of the individual production modules is based, among other things, on the technological possibilities of the potential users, the technological boundary conditions resulting from the material used and, last but not least, the forecast market-related cost requirements. The overarching objective of the developments is to enable the production of a joined bipolar plate of the correct quality in less than 1 second.
Fraunhofer IWS Contribution
Continuous Inline Joining to Bipolar Plates / Laser Roll Welding with Roll Bonding Process
The aim is to map the R2R process of roll gap-based joining together with adhesive bonding technology for the first time in a corresponding demonstration plant for multi-beam high-speed joining of BPP. For this purpose, both multi-beam laser gap welding and BPP seal bonding will be technologically advanced and prepared for high-rate production. The synchronization of the process steps together with the strip feed are major challenges. Another focus is on online process control for quality assurance. As a result, a plant prototype for joining as well as a BPP demonstrator will be created.
In order to fulfill this task, an existing laser roll cladding stand will be upgraded, in addition to the mandatory expansion of existing system components, to the extent that strip speeds ≥ 30 m/min with strip widths of up to 145 mm can be realized.
As a result, both a significant increase in achievable cycle times for the production of BPP and economic efficiency through significant reduction of scrap compared to current joining processes will be made possible. With the completion of this project, a technology maturity level of TRL5 to TRL6 will be achieved for the submodule of roll gap-based multi-beam laser gap welding with combined roll bonding process.
Continuous Coating for Bipolar Plates / Continuous Vacuum Coating
The aim is to further develop the equipment and process technology of vacuum coating from a batch into a high-rate strip coating process. For this purpose, an existing and proven highly efficient coating system will be transferred to the strip coating line (strip speed 10 m/min, strip width 300 mm). In-house profitability calculations comparing batch and strip processes, as developed in this project, showed a possible reduction in coating costs of up to 90 % per BPP through strip coating. This was calculated for a possible output of approx. 2.5 million BPP per year (strip width 300 mm and strip speed 10 m/min). Furthermore, a scaling concept for belt speeds of 50 to 100 m/min. or wider belt and a corresponding profitability calculation will be carried out. This is expected to result in additional cost savings. A further goal is the development of a 100 % and full-surface AI-based inline process control for coil coating on a strip width of 300 mm.
If the project is successful, the result will be a considerable reduction in the cost of coatings and an increase in material efficiency by reducing the necessary coating thickness. The concept envisaged here is suitable for setting up future mass production.
Continuous Inline Cutting Out and Free Cutting of Bipolar Plates / High-speed Cutting Using CW Lasers
The aim is to further develop the cutting and separation processes for the continuous production of BPP, starting from technology maturity level 4 up to technology maturity level 6. The result is the demonstration of all necessary separation steps in the production of BPP with at least the process speed of upstream process steps. The demonstrator enables the virtual linking of the production chain as well as the physical separation of the semi-finished products produced in previous process steps with the specifications defined in the production design, so that the result is semi-finished products that can be evaluated in terms of quality and quantity.