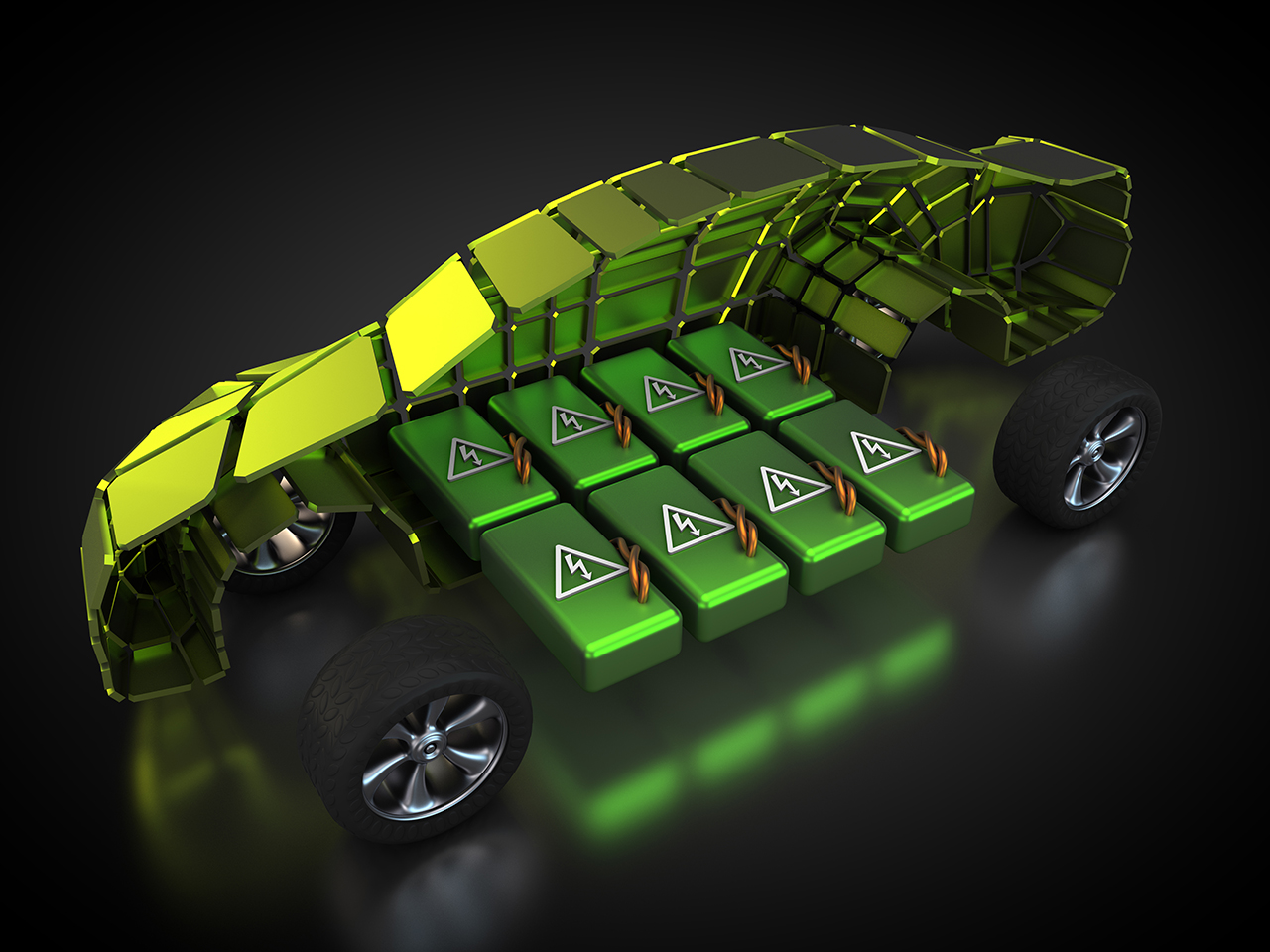
As a result of the increasing electrification of mobile drives, the use of modern copper and aluminum materials is steadily gaining in importance. Due to their high electrical conductivity, they are excellently suited for the transmission of electricity. Conventional joining processes such as gas-shielded metal arc welding (GMAW) or tungsten inert gas welding (TIG) are more and more reaching their limits in view of the advancing miniaturization of components and parts as well as increasing quality requirements for joined joints.
Laser beam welding, characterized by the concentrated energy input into the component, offers a superior process for the production of similar (e.g. copper-copper) and dissimilar (e.g. aluminum-copper) welded joints. By means of high-performance laser beam sources, high power densities can be realized, resulting in joints with excellent weld seam quality even on highly reflective and coated material surfaces.
The advantages of laser beam welding
Material
- Joining of highly reflective and coated materials
- Joining of thin foils from a few micrometers thickness to thick sheets
Process
- Cost-effective joining processes that can be fully automated
- Heat input control via process parameters to reduce intermetallic phases
- Avoidance of process spatter during welding
- Use of image recognition software for continuous welding process optimization
Component properties
- Low thermal stress on the component during the welding process
- Metallic joints with high electrical conductivity, e.g. low transition resistances, optimal contacting
- Production of components with long service life and optimum joint geometry while preserving important material properties, e.g. mechanical stability under vibration and acceleration
Application examples
- Batteries: Cell housings, cell connectors, current collectors, contact and bus bar connections
- Electric motors: Hairpins, shunts, cables, copper strands, cable connectors
- Peripherals: electrical contacts, power electronics