Glued laminated timber made of Robinia from lignite recultivation areas and dry sites in Saxo-ny/Brandenburg (ROBINIA)
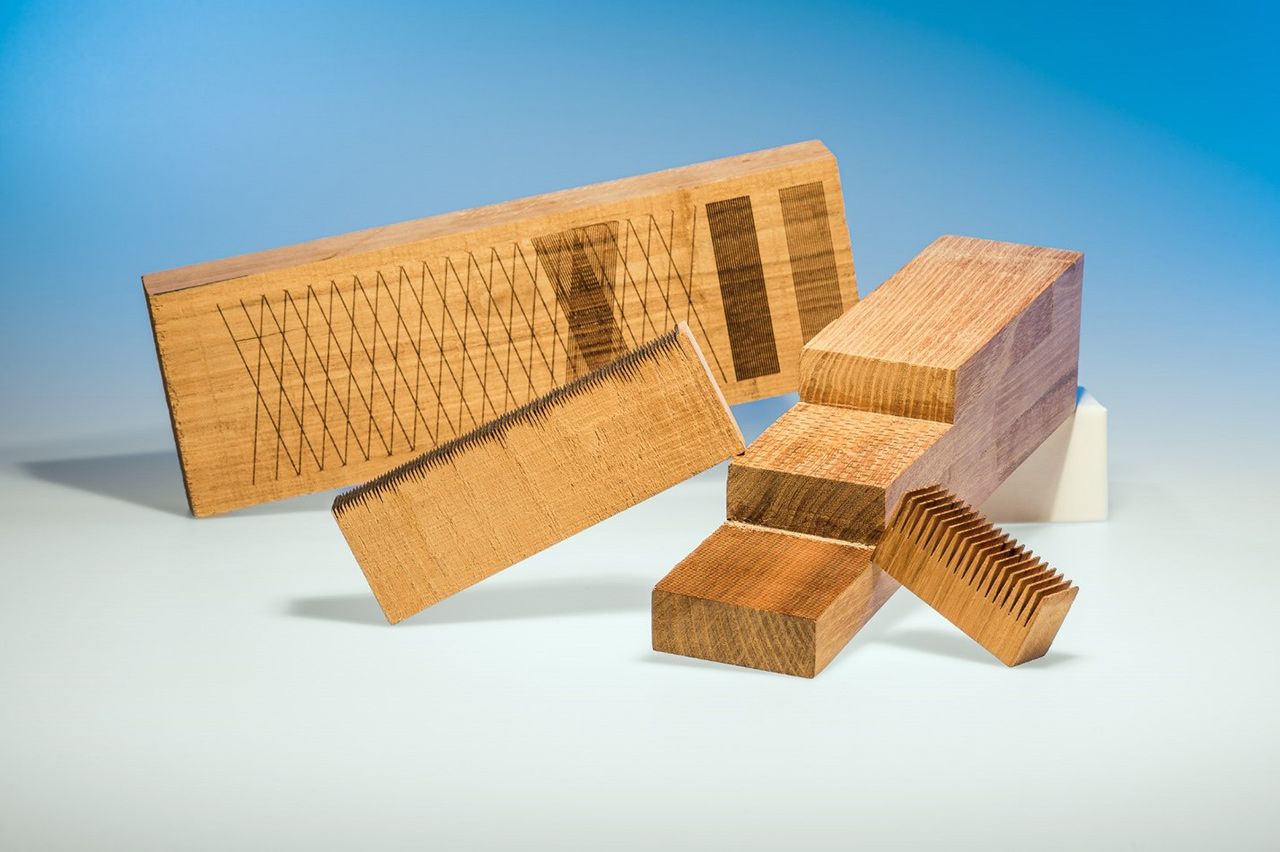
Motivation
Outdoor timber constructions offer great potential for saving CO2 by substituting materials like concrete and steel, while binding atmospheric CO2 in the cell structure. The hardwood of the fast-growing Robinia (Robinia pseudoacacia) is characterized by good mechanical properties and high resistance to moisture, heat, cold and pests. This makes the wood predestined for the application in outdoor load-bearing structures such as bridges or towers of wind power plants. Since the drought and heat resistant Robinia also grows on nutrient-poor soils, it naturally occurs as a pioneer tree and thus offers the opportunity for climate-resistant, soil-stabilizing reforestation and forestry use of abandoned open-cast mines.
An economical usage of the wood of the Robinia for building load-bearing structures, requires homogenous properties aswell as geometric dimensions, which can only be achieved by combining wood lamellas to glued laminated timber (glulam). Since the surface the wood is very dense and has a large number of extractives, the wood is considered difficult to bond adhesively. The economic production of glulam is also hindered by the long curing times of the adhesives aswell as the high abrasion of the cutting tools used to cut out finger joints for longitudinal bonding in the end grain of each lamella.
Objective and solution approach
In joining technologies surface pretreatment is currently mainly used as preparation for subsequent bonding. In terms of their effect, surface pretreatment processes can be classified into processes for changing the surface topology and processes for changing the chemical structure. Plasma treatment improving the bondability of wood and thermoplastic matrices has already been proven in the past. In addition, the use of laser and plasma sources showed great potential for the production of wood-metal composites. Surface pretreatments will therefore be incorporated in the manufacturing process of glulam made of Robinia wood.
In order to minimize the long curing times of conventionally used adhesives, the wood lamellas are joined using a thermoplastic matrix obtained from granulated CFRP waste from the automotive and aerospace industries. The carbon fibers present in the granules can be inductively heated due to the electrical conductivity of the fibers, melting the thermoplastic matrix indirectly and thus enabling an adhesive bond (thermal direct joining). Using this technology, processing times are reduced from several hours to a few minutes or even seconds.