Generative laser powder buildup welding
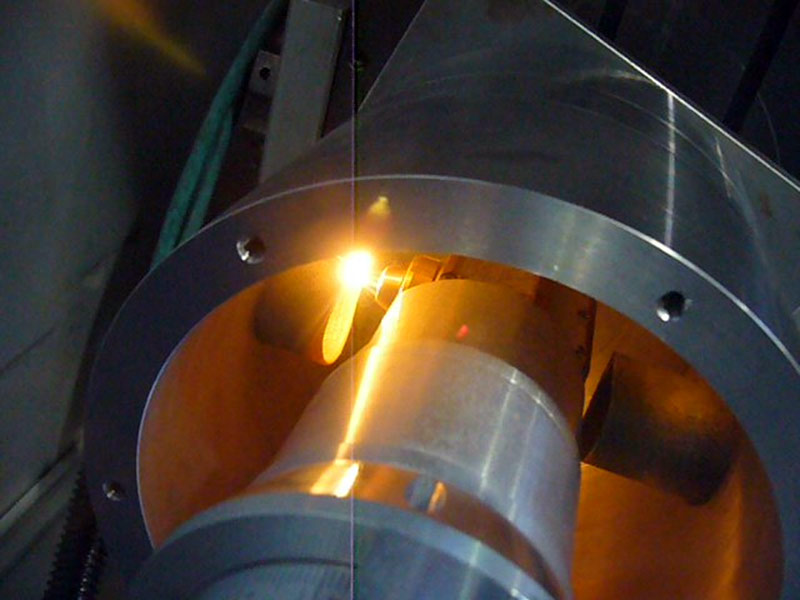
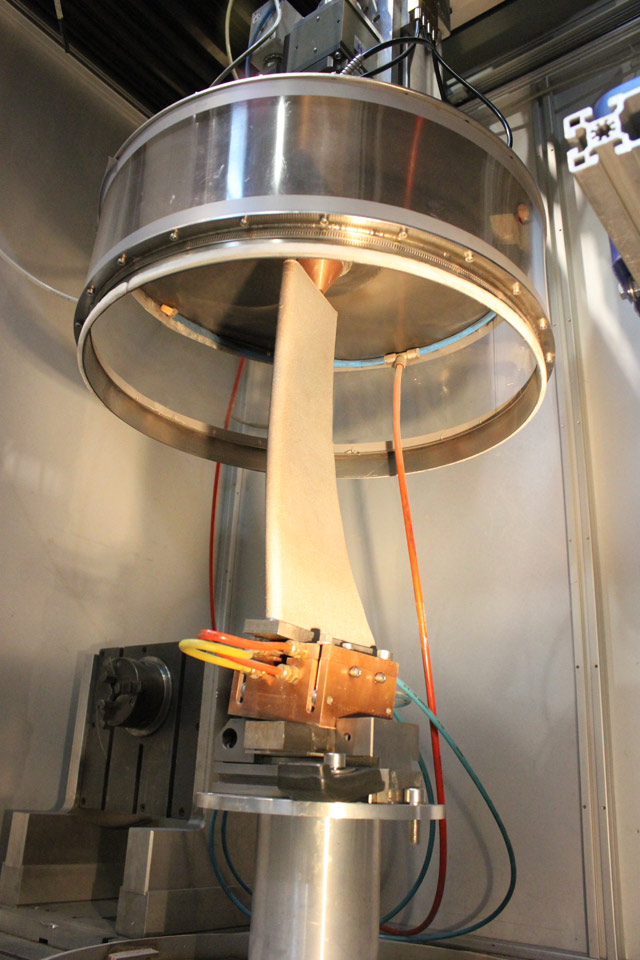
Based on 3D-CAD data models, 3D structures are generated for the direct fabrication, modification or repair of components. The component size is unlimited in this procedure and the smallest lateral resolution is 30 µm. Steels, nickel and cobalt alloys, titanium and aluminum lightweight materials and carbide composites can be processed in a defect-free manner. Currently IWS scientists focus their research into the development of intermetallic titanium aluminides and Ni-based high temperature materials.