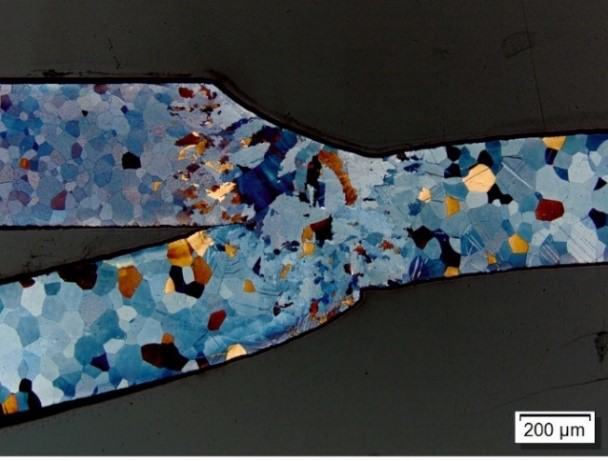
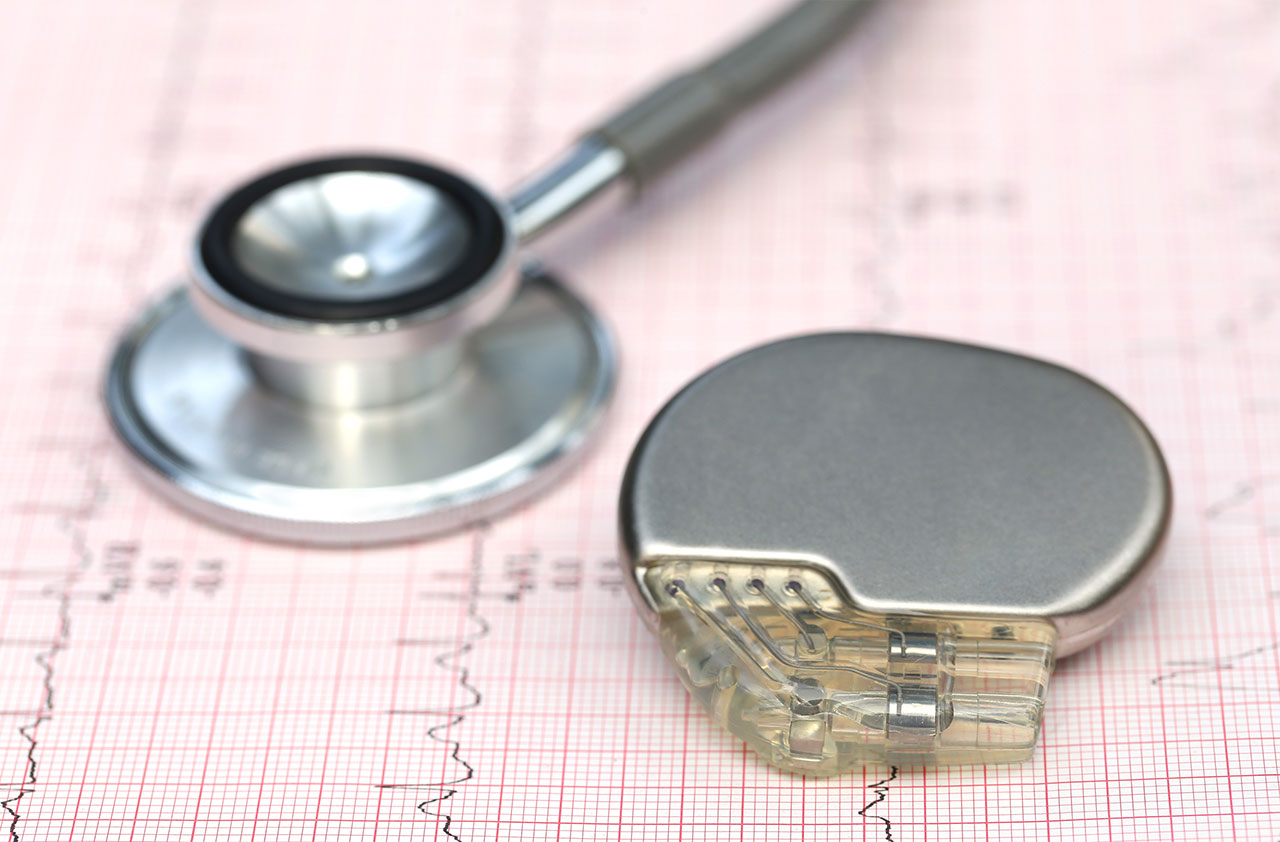
Biocompatible and corrosion-resistant materials such as titanium and stainless steel are the preferred materials for use in medical engineering. Specific requirements for the properties of welded joints result from their use on or in the human body. These include, in particular, their tightness and surface quality. Consequently, thermal surface damage such as oxide formation must be avoided during the joining process. Welding under an inert gas atmosphere in a clean laboratory environment not only ensures compliance with hygiene standards, but is also a key factor in reducing the risk of residues on surfaces such as material spatter. Intelligent (real-time) process monitoring is the key to continuous quality assurance and documentation.
Advantages of laser beam welding
Material
- Suitable for metallic materials and additively manufactured components
Process
- Fully automatable and contactless joining technology
- Excellent control of energy input into the part by 2D scanner technology
- Seam detection and process monitoring by inline and offline sensors, e.g. optical image recognition, plasma detection, acoustics, ultrasound
- Process suitable for series production - small and large batch sizes can be realized
Component properties
- Crack-free welded joints even without filler metals
- Low-damage joining process due to low heat and energy input into the component
- High reproducibility with maximum possible quality, e.g. homogeneous, smooth seam surfaces and properties
- Avoidance of biorelevant contamination due to low surface roughness
Application examples
- Hermetically sealed joint for medical instruments and implants
- Welding of half shells for cardiac pacemakers made of titanium
- Non-ferrous metal-copper joints or brass, e.g. gas fittings for oxygen supply
- Aluminum welded joints for imaging components, e.g. X-ray chambers