Coating system Multi-Sputter-Lab 600 (MSL600)
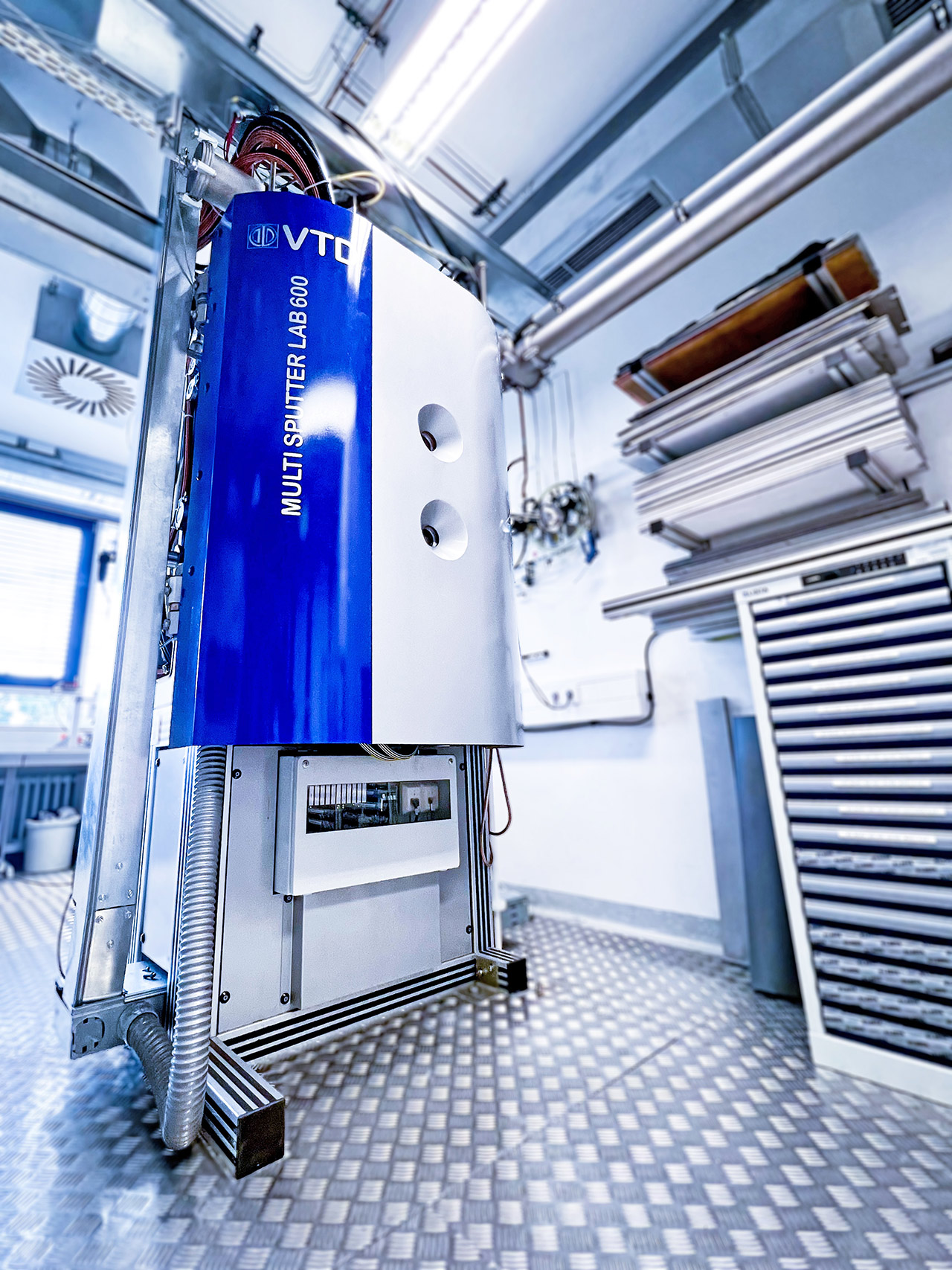
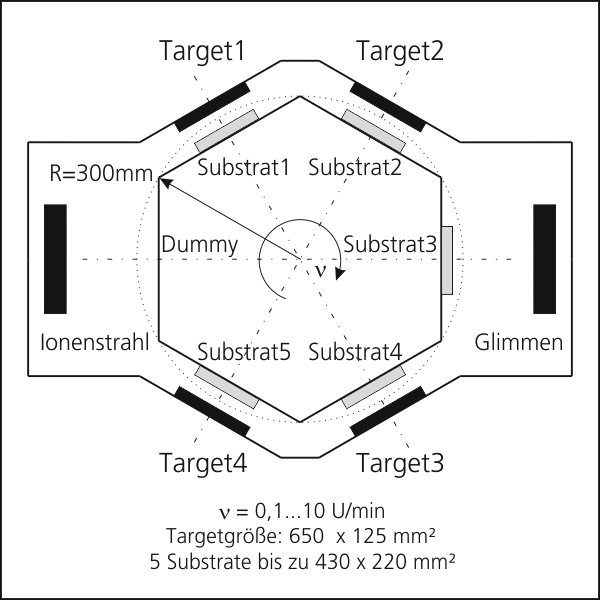
Reactive multilayer systems (RMS) are produced via PVD processes, such as magnetron sputtering.
Magnetron sputtering offers the advantages of precisely controlled manufacturing, as well as the ability to scale up for high volume production. With the Multi-Sputter-Lab 600 (MSL600 of the manufacturer VTD Vakuumtechnik Dresden GmbH) it is possible to produce free-standing RMS foils for mobile applications as well as to coat components over their entire surface or in a structured manner.
The MSL600 has four magnetron coating sources, which can be operated with powers of up to 10 kW, and two substrate cleaning stations. In addition to RMS deposition, it is thus possible to carry out pre-cleaning steps such as smoldering or ion beam etching as well as the deposition of solder and wetting layers.
Up to five components or RMS with dimensions of up to 430 x 220 mm2 can be homogeneously coated on a six-fold polygon substrate carrier arranged in the center of the coating sources. At maximum capacity, RMS with an area of up to 4730 cm2 can be produced in a single pass. Substrate cooling ensures reliable heat dissipation from the components to be coated as well as a high energy yield from the RMS produced.