More Energy Efficiency in the Process Chain – Expanding the Range of Applications for Naturally Hard Martensitic Sheet Steel by Further Developing Production Technologies
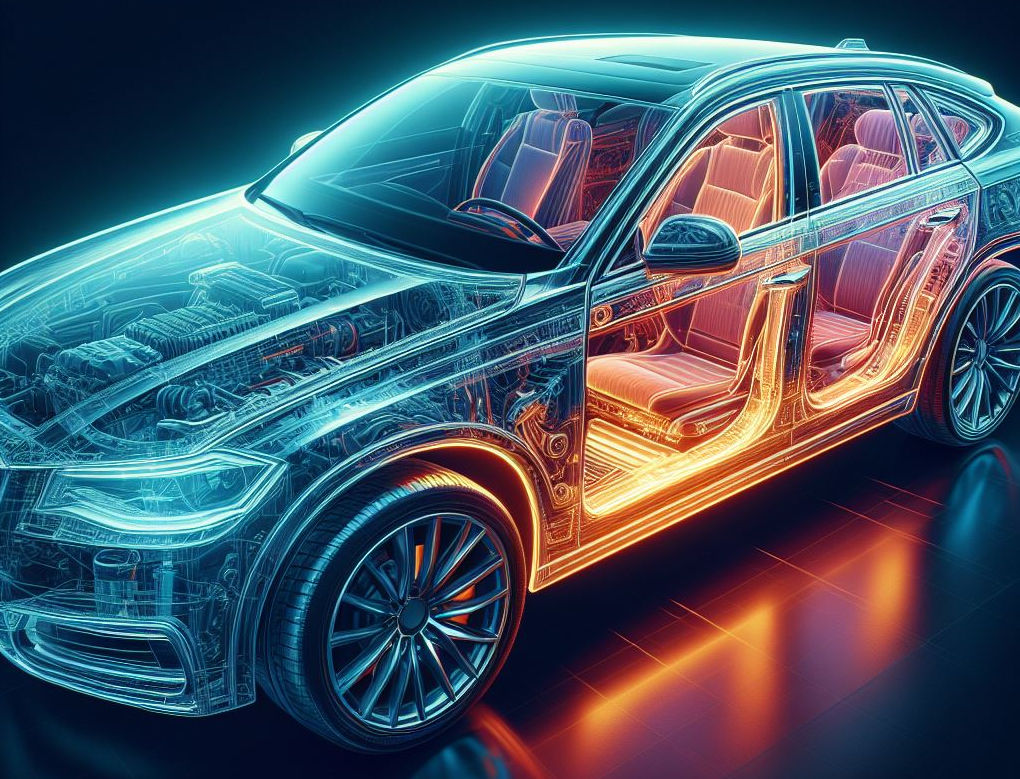
Motivation
Lightweight construction is a key starting point for saving energy in the operation of a vehicle. The manufacturing process of the material is also included in the consideration of the overall energy efficiency of mobility.
Steel is an established lightweight material in the mass market. Fiber-reinforced plastics (FRP), on the other hand, are mainly used in high-performance applications.
In terms of the energy required, the materials used differ considerably. Compared to an aluminum or FRP body, the production of a corresponding steel body requires only about one third or one sixth of the energy required. The use of naturally hard, martensitic steels instead of the boron-manganese steels currently used opens up further potential for savings in the production of load-bearing structural components. Both steels consume a similar amount of energy during production. However, when using naturally hard, martensitic steel, the press-hardening process can be dispensed as an additional process step and thus the energy required for this.
Compared to fiber composites, steel also has a high recycling rate (~100 %), which reduces the use of iron on the one hand and brings a further 35 % reduction in energy requirements on the other.
Aims and Procedure
The currently missing technologies (cutting, forming, joining) for the large-scale use of the martensitic material for structural components in automotive construction are to be developed as part of the PROMAR project. If the technology is introduced in its entirety, there is a real savings potential of 40 GWh per year for the production of steel car bodies in the selected application case throughout Germany, which corresponds to the average electricity consumption of approx. 13,000 households.
The energy requirement for processing technologies can be reduced in both forming and laser welding. In addition, the introduction of a laser process in cutting can enable the use of conventional cutting material for small components, which increases material utilization.
Perspectives and Innovations
The trend underlying the project – steel as a lightweight material and its energy-efficient processing – is to be further advanced with the processing technologies to be developed in the project and their transfer to industry.