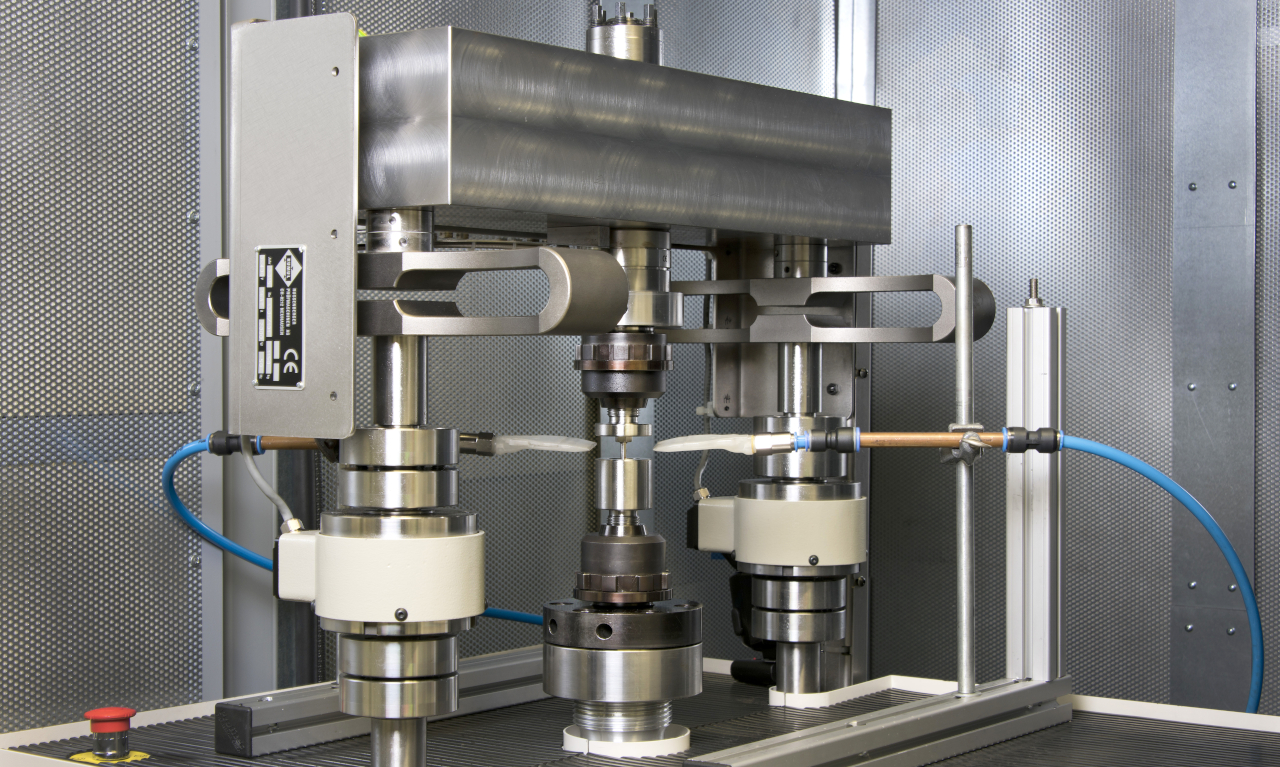
The reliability of components is a central aspect in the qualification of new manufacturing processes with resource-efficient material use. In this context, the focus is on fatigue properties, the experimental verification of which is often the bottleneck for the transition from development to series production. With its modern high-frequency testing laboratory, Fraunhofer IWS offers a wide range of possibilities for a rapid strength assessment of materials and components and thus creates a previously unattainable reduction in the necessary testing times.