Review on the award of the German Future Prize 2020 (Deutscher Zukunftspreis 2020) to Trumpf, Zeiss and Fraunhofer
EUV lithography opened the door to digital age
Optical lithography has been considered a key technology for microchip production for more than 40 years. The new development towards EUV lithography extended the limits of the classi-cal technology by far. The Fraunhofer Institute for Material and Beam Technology IWS contribut-ed to the fact that now the Fraunhofer-Gesellschaft, ZEISS and TRUMPF have been awarded the “ Deutscher Zukunftspreis 2020”. The project "EUV Lithography – New Light for the Digital Age" focuses on the manufacturing method of the latest EUV microchip generation. Along the way to this success Fraunhofer IWS, together with Fraunhofer IOF and Fraunhofer ILT, has established several milestones in recent decades.
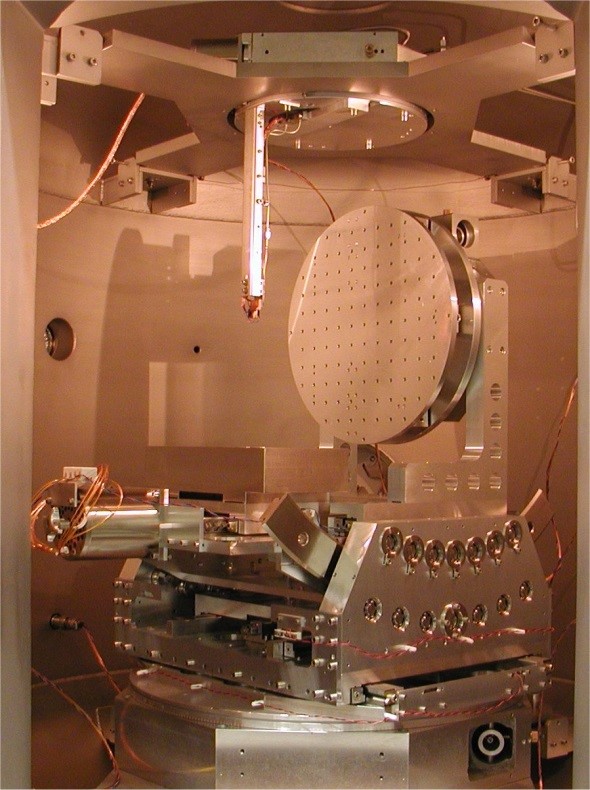
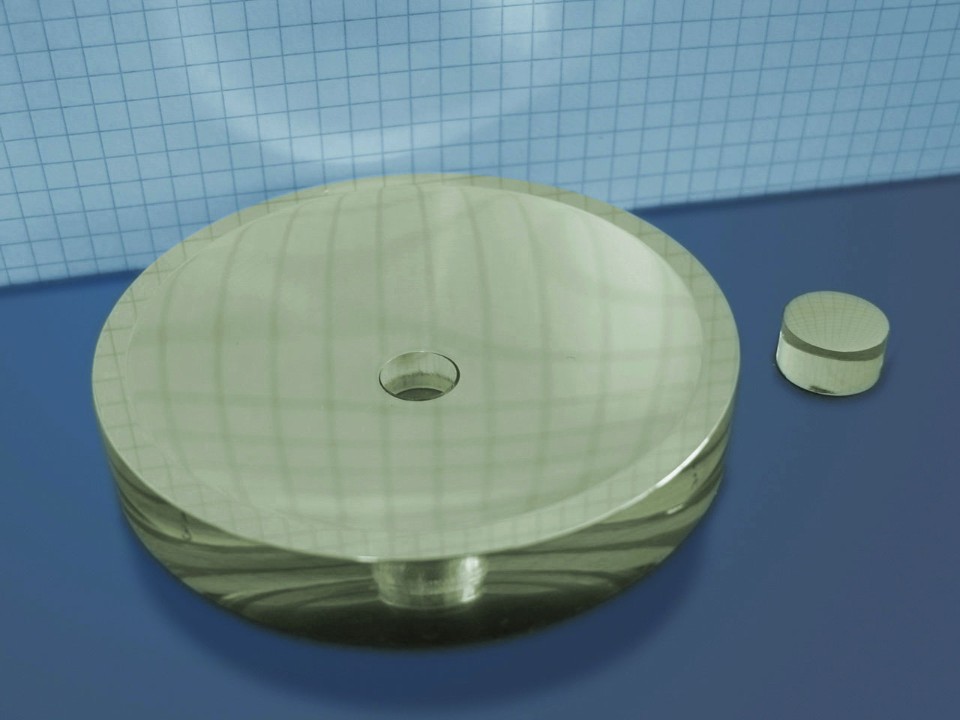
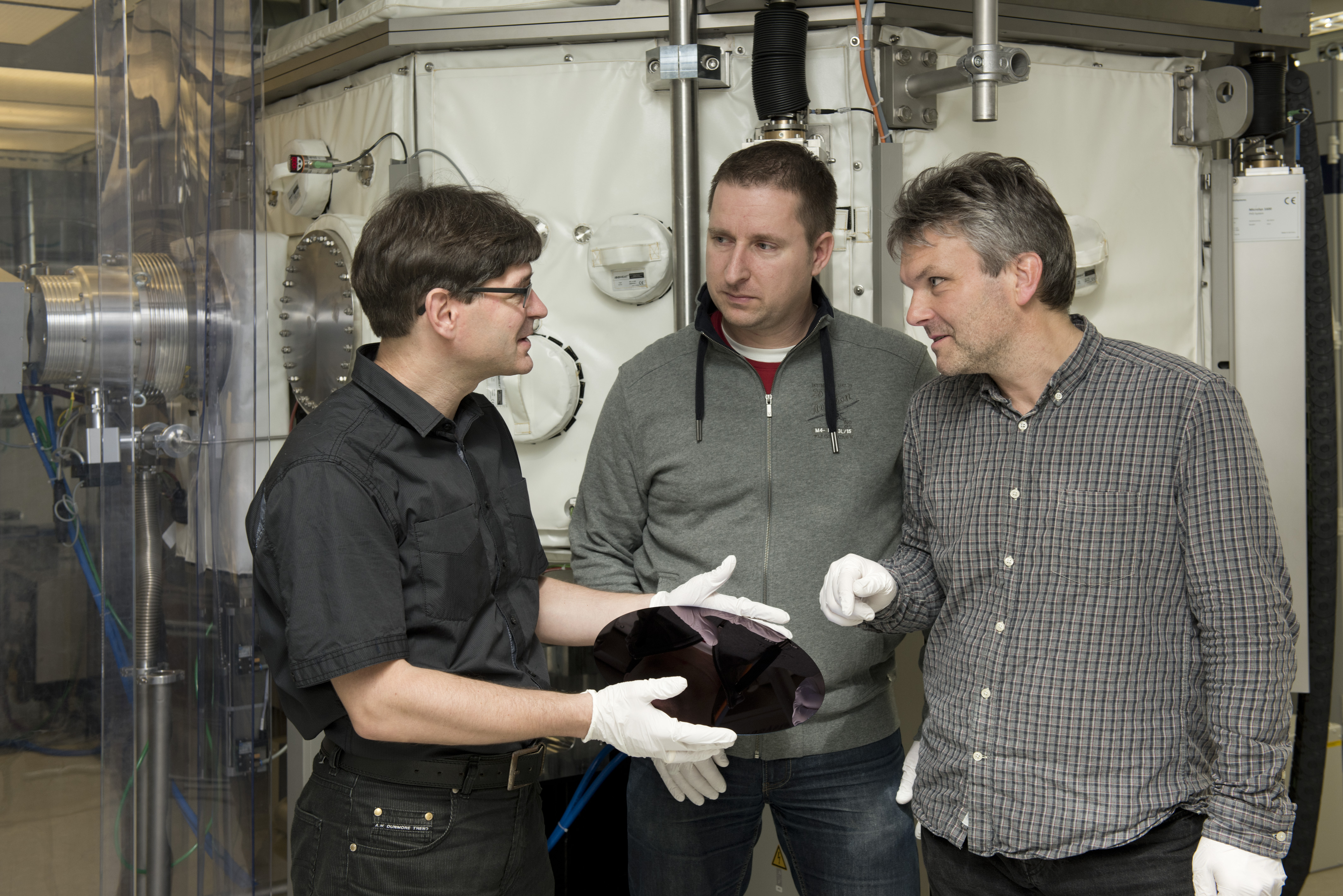
EUV lithography shows a long history within the Fraunhofer-Gesellschaft. The technological development results from a collaborative effort: In the Fraunhofer network ”Light and Surfaces“, Fraunhofer IWS, IOF and ILT are jointly researching various sub-aspects of the new technology, in particular the optics and light sources required for EUV radiation. For more than two decades Fraunhofer IWS has been concentrating on the production of reflective optical coatings. EUV mirrors consist of precise nanometer multilayer systems, which the researchers apply to large, complex-shaped surfaces, always with the aim of achieving the best possible reflectance levels and lowest scattering losses.
New techniques and first records: The early days
Already in the 1990s Fraunhofer IWS developed several coating processes to produce multilayer mirrors for the soft X-ray and EUV wavelength range. Peter Gawlitza regards the introduction of the state-of-the-art magnetron sputter coating technology at the Dresden institute in 2000 as a major milestone in the development of coatings for EUV mirrors. The group manager of the team EUV and X-ray optics emphasizes that, for the first time, it was possible to produce high-quality coating stacks precisely, reproducibly, extremely smooth and relatively fast. The research team, of which Gawlitza was already a member at that time, thus produced layers with an EUV reflectance of more than 70 percent first in 2001: at that time the world record for EUV mirrors. Gawlitza points out: ”The world record layers were of course produced under idealized laboratory conditions on small, flat model samples. For actual applications, other factors such as thermal stability or complex mirror geometry are important, so these values cannot be achieved for all applications. Nevertheless, best reflectance values are always an indication of the excellent coating process quality“. In the following years, the institute achieved further records with continuous advancements of the coating process.
First laboratory EUV reflectometer in Europe
Measuring the optical properties of the mirrors at the application wavelength also plays an important role in the coating development. To this end Fraunhofer IWS engineers constructed the first EUV laboratory reflectometer in Europe in 2002. The device is able to measure the coated mirrors with EUV radiation, dependent on angle and wavelength, and thus determine the optical properties of the surface coating. Until then, all this was usually only possible with a synchrotron radiation source. ”Synchrotron beam time is extremely expensive at large-scale research facilities and access is limited,” says Peter Gawlitza, explaining the disadvantages. On the other hand, the EUV reflectometer generates the EUV radiation with a laser pulse plasma source on a laboratory scale and therefore is easily, quickly and flexibly available for the metrology of EUV mirrors. The very first EUV laboratory reflectometer is still in use today, 18 years later, and is a constant tool in the research of EUV mirror coatings.
EUV microscope with Schwarzschild-type reflecting objective
The newly developed EUV coatings for optical devices are also of great interest beyond the field of semiconductor lithography. Based on the joint results, Fraunhofer IWS researchers and colleagues from Fraunhofer ILT designed an EUV microscope in 2004 containing an EUV source, collector optics and a Schwarzschild objective. Fraunhofer IWS provided the reflective coatings of the cylinder-like collector optics and the two spherical mirrors of the Schwarzschild objective. Advanced polishing methods and mirror coatings have led to a new type of Schwarzschild objective, especially for EUV radiation at 13.5 nanometer wavelengths. As in microscopy, this type of optics can be used to obtain a magnifying image of a test object. However, it can also be used upside down as a miniaturizing optics, for example to focus a spatially extended EUV source on structures of few nanometers in size.
Joseph von Fraunhofer Prize honors scientists’ achievements
In the following years, many developments for process stabilization and scaling to large mirror geometries were required for the industrial implementation of the EUV coating technology. The first significant industrial EUV mirror coating system concept was designed by Fraunhofer IWS in 2010. This system had six linear coating sources and was able to coat mirrors with a diameter of up to 600 millimeters. The work to further develop the EUV technology and to design prototypes for industrial systems paid off in 2012 when Fraunhofer IWS together with Fraunhofer IOF and Fraunhofer ILT were awarded the Joseph-von-Fraunhofer Prize for outstanding scientific achievements. The three group managers of EUV lithography at that time – Dr. Stefan Braun (IWS), Dr. Klaus Bergmann (ILT) and Dr. Torsten Feigl (IOF) – accepted the award on behalf of their institutes.
Further developments and milestones after 2015
Starting in 2015, Fraunhofer IWS achieved further milestones in coating research for EUV lithography: It surpassed the own peak reflectance value and achieved the still valid world record for EUV mirrors of 70.8 percent for 13.5 nanometers with normal incidence reflection. At the same time, the demands on EUV lithography systems have developed rapidly, in particular the optical surfaces to be coated are increasing in size and are in part strongly curved. For the coating process, these requirements imply precise and steep thickness gradients, sometimes varying over the stack height. Peter Gawlitza says:”The transfer of coating technology to large, complicated surfaces is one of our main successes. We have significantly improved the coating of large optics since 2015 so that we can now produce aspherical or asymmetrical mirror surfaces with the highest degree of reflection“.
Goals and achievements
The microchips produced by means of EUV lithography have reached mass production level since the end of 2018. Leading smartphone manufacturers launched the first models with EUV-exposed processors in summer 2019. These new-generation smartphones now contain processors that are more functional, more energy-efficient and faster than all their predecessors. And research development is far from complete: Further structural reduction steps have already been included in the scope of worldwide lithography re-search. The Fraunhofer Institute for Beam und Material Technology IWS continues to be active in this field and regularly participates in national and international projects on EUV lithography, such as the current EU project ”TAPES3“. In this joint project, the partners are working on lithography technology for structure sizes of three nanometers until the end of 2021. ”Light exposure processes are becoming more and more sophisticated, the optics correspondingly more complicated and less regular. Nevertheless, the optics have to be smooth and perfectly coated – moving the technology to that point is our current task,” concludes Peter Gawlitza. The teams awarded the ”Deutscher Zukunftspreis” have significantly contributed to the further development of EUV lithography in their expertise fields. However, research on this topic is far from complete. EUV group manager Gawlitza is very happy about the increased public awareness of the topic since the nomination. People at Fraunhofer IWS warmly congratulate the prize winners and their teams on this great award.