Dynamic beam modulation for the optimization of industrial laser processes (FastShape)
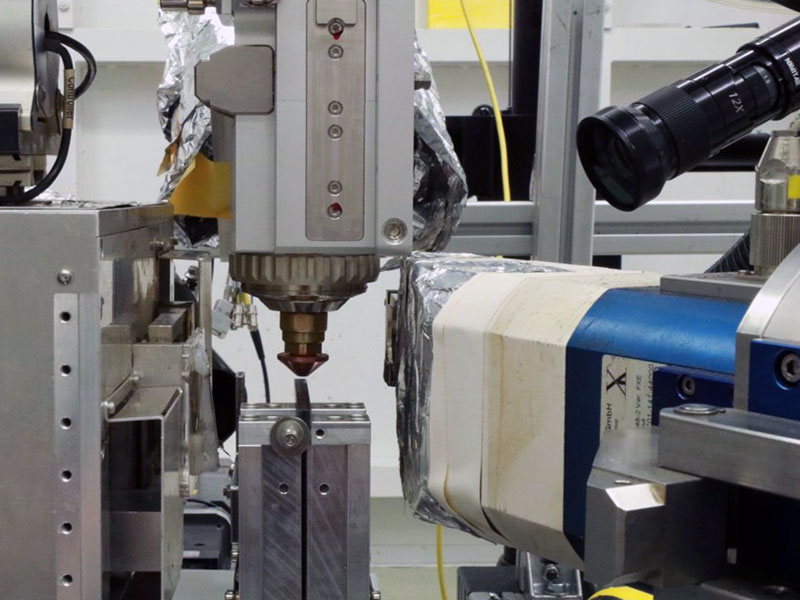
Motivation
Laser cutting and welding have been considered industrially established processes for decades. However, for neither of them a complete model-based process image exists that reliably predicts the effect of a parameter variation on the process behavior. Process developers and users therefore continue to rely on experimentation to develop and optimize new processes. On the one hand, this approach takes a lot of time, on the other hand, the results cannot be generalized for global problems. What is considered to be true for the classical process variants applies even more to the new ones with superimposed beam oscillation.
In both cutting and welding with superimposed beam oscillation, the first applications are already being realized in industrial production. An exponential spread of the process variants fails because of the complex process development described above and is therefore only used when the classic process approach is not effective. The saving potentials for all applications realized in the classic process approach thus remains unexploited.
The brake on innovation is the incomplete understanding of the process. In the case of laser welding with beam oscillation, it is therefore not possible to make targeted adjustments in the event of incomprehensible process changes. In the case of laser cutting, rapid adaptability to different materials, material thicknesses, beam quality and laser powers is required, which is also currently not possible.
Aims and procedure
In cooperation with the project partners, this brake on innovation is to be solved. By means of insitu diagnostics, an understanding of the process is to be achieved that will help to understand the effects achieved by superimposed beam oscillation and to apply them in a targeted manner.
Future prospects
The companies thus gain more security for the introduction of the innovative technology for laser cutting and welding with superimposed beam oscillation and can react solution-oriented to changes in the boundary conditions, which significantly increases the acceptance on the part of the end users.