Dynamische Strahlmodulation zur Optimierung industrieller Laserprozesse (FastShape)
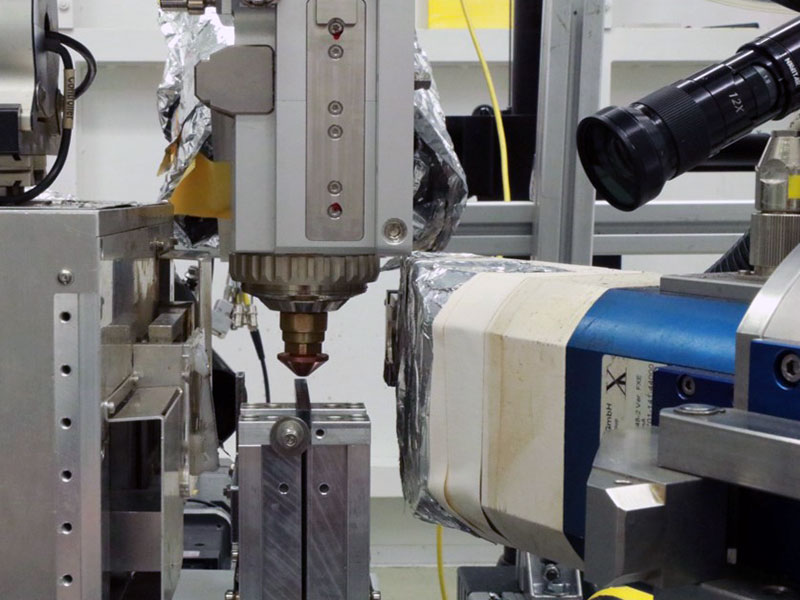
Motivation
Laserschneiden und –schweißen gelten seit Jahrzehnten als industriell eingeführte Verfahren. Für keines der beiden existiert jedoch ein vollständiges modellhaftes Prozessabbild, welches zuverlässig die Auswirkung einer Parametervariation auf das Prozessverhalten vorhersagt. Prozessentwickler und Anwender sind somit weiterhin auf das Experiment angewiesen um neue Prozesse zu entwickeln und zu optimieren. Diese Herangehensweise nimmt zum einen viel Zeit in Anspruch, zum andern lassen sich die Ergebnisse nicht für globale Fragestellungen verallgemeinern. Was für die klassischen Prozessvarianten gilt, betrifft umso mehr die neuen mit überlagerter Strahloszillation.
Sowohl im Schneiden als auch Schweißen mit überlagerter Strahloszillation werden bereits erste Applikationen in der industriellen Fertigung realisiert. Eine exponentielle Verbreitung der Prozessvarianten scheitert an der beschriebenen aufwendigen Prozessentwicklung und kommt somit zumeist nur zum Zug, wenn der klassische Prozessansatz nicht zielführend ist. Die Einsparpotentiale für alle bisherigen nach klassischen Prozessansatz realisierten Anwendungen bleiben somit unerschlossen.
Innovationsbremse ist das lückenhafte Prozessverständnis. Im Falle des Laserschweißens mit Strahloszillation kann somit bei nicht nachvollziehbaren Prozessänderungen nicht gezielt nachgeregelt werden. Beim Laserschneiden ist eine schnelle Anpassbarkeit auf unterschiedliche Werkstoffe, Materialstärken, Strahlqualität und Laserleistungen erforderlich, was aktuell ebenfalls nicht möglich ist.
Ziele und Vorgehen
In Zusammenarbeit mit den Projektpartnern soll diese Innovationsbremse gelöst werden. Mittels Insitu-Diagnostik soll ein Prozessverständnis erreicht werden, dass hilft, die erzielten Effekte der überlagerten Strahloszillation zu verstehen und diese gezielt an zu wenden.
Perspektiven
Die Unternehmen erhalten somit mehr Sicherheit für die Einführung der innovativen Technologie für das Laserschneiden und –schweißen mit überlagerter Strahloszillation und können lösungsorientiert auf Änderungen der Randbedingungen reagieren, was die Akzeptanz seitens der Endanwender signifikant erhöht.