Six Fraunhofer institutes have made technological leaps forward in systems engineering, materials and process control as well as end-to-end digitalization / 2020
Fraunhofer Lighthouse Project futureAM Gets Metallic 3D Printing in Shape for Industrial Use
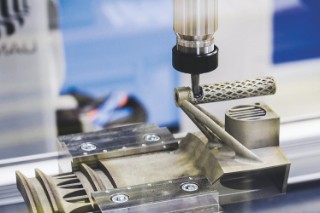
Accelerating the additive production of metal components by at least a factor of 10: With this goal in mind, the Fraunhofer-Gesellschaft launched the lighthouse project “futureAM – Next Generation Additive Manufacturing” in 2017. As the project ends in November 2020, six Fraunhofer institutes have made technological leaps forward in systems engineering, materials and process control as well as end-to-end digitalization, thus increasing the performance and cost-effectiveness of metal-based additive manufacturing along the entire process chain.
more info