Laser-based manufacturing method of bimetalc semi-finished products for solid plain bearings for use in large components (LaserPlatt)
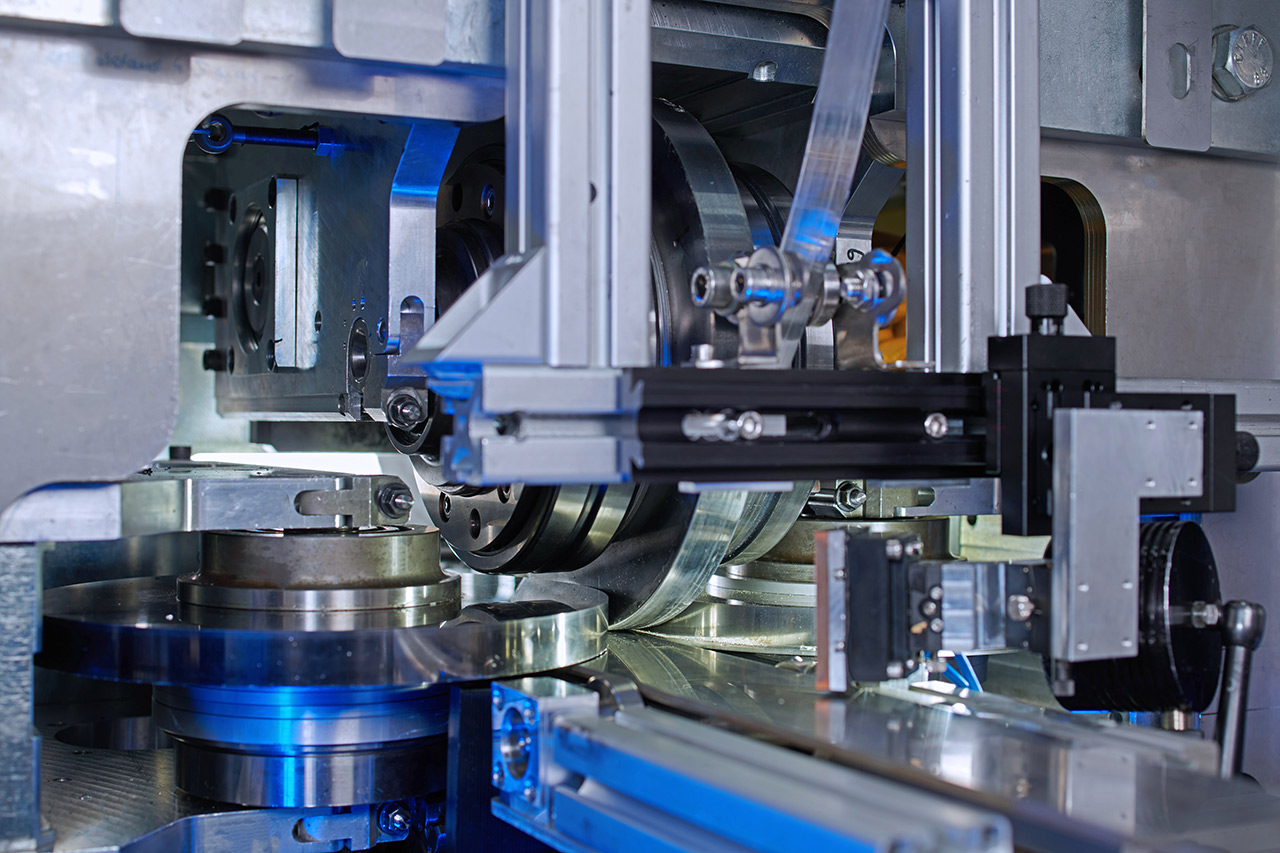
Motivation
Plain bearings are indispensable for many applications in common mechanical engineering, the automotive industry and aviation. They have to meet very different requirements there, such as strength, wear resistance and temperature resistance. To meet these, plain bearings are usually made from bimetals, a combination of two different metals. At present, small batches are manufactured by using strip or blanks. In this process, special bearing materials are melted, cast into small blanks and further processed into suitable semi-finished products in many individual production steps. For the area of special and large bearings, very small batch sizes present a particular challenge because the use of strip as a starting material is not economically viable here due to the small quantities involved.
Objectives and Approaches
The aim of the project LaserPlatt is to develop a significantly more effective and flexible manufacturing technology for bimetal semi-finished products in previously unfeasible thickness combinations, especially in the combination of steel and aluminum-silicon bearing materials. The starting point is the technology of laser roll cladding, which is being technologically further developed with regard to the materials and semi-finished products to be combined. Besides the industrial application, the project focuses on topics of new material combinations. The aim of the project is to build a prototype plant to demonstrate the feasibility of the process.
Until now, laser roll cladding has only been used for narrow, strip-shaped bimetals. The new process takes advantage of the laser beam, which, formed into a line, heats only the inner surfaces of the metal strips at the joint. This drastically reduces forming and, in conjunction with rapid cooling in the joining zone, allows greater thicknesses of different material pairings to be combined. The process speed can be significantly increased by additional inductive preheating. The effort required for pre-treatment and post-treatment is thus significantly reduced. For the intended purpose, the process must be qualified with regard to thermal process control for processing different melting temperatures. Furthermore, special machine requirements, such as a horizontal feed and the optimum design of the laser contact zone, must be met and implemented as a prototype.
Applications and Results
In the future, this new process will make it possible to meet demands for greater overall thicknesses of semi-finished products, especially for large engines. This will open up new opportunities for engine manufacturers to use large plain bearings, for example in power generation. The innovative products and access to new market segments will improve and expand the competitive position of the SME involved.