Development of technical processes for direct thermal joining within short process times of metal-plastic hybrid joints in lightweight construction applications (TheDi)
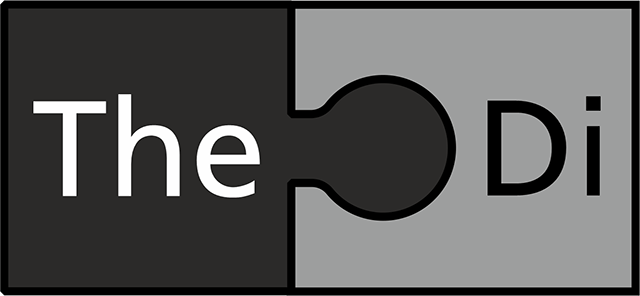
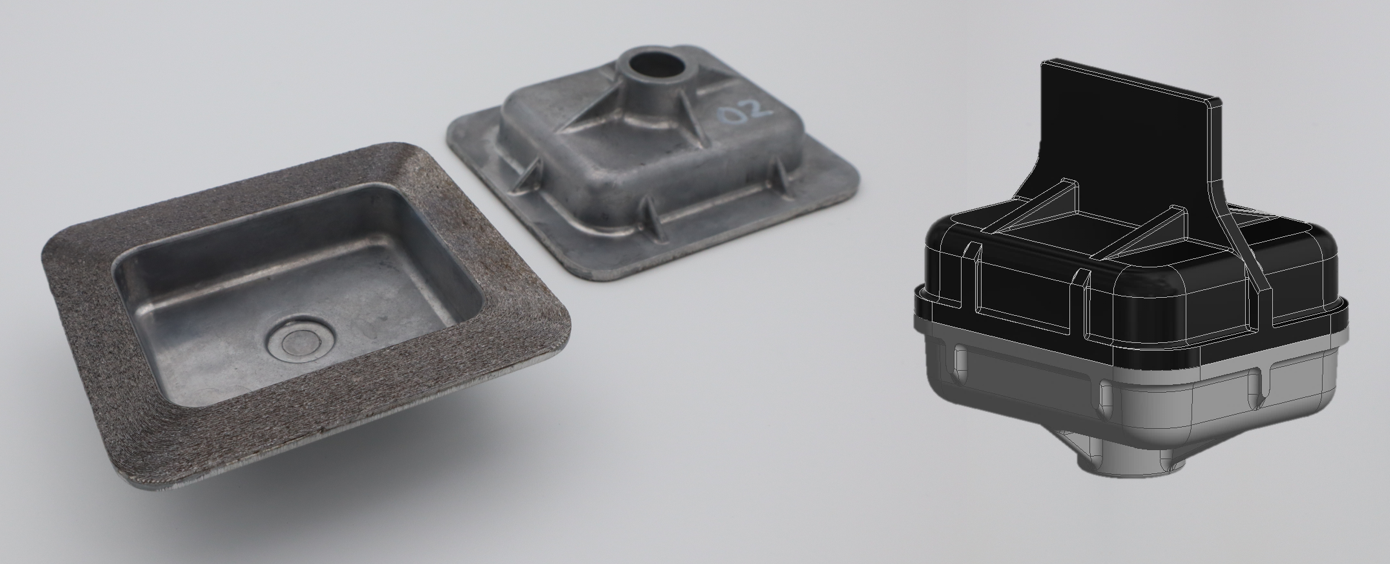
Motivation
Currently, the majority of technically used metal-plastic hybrid joints are produced by injection molding, mechanical joining processes (pressing, screwing, riveting, clinching, etc.) or adhesive bonding. However, each of these processes has significant intrinsic disadvantages. In the case of the injection molding approach, for example, the application is usually only economical for large series, since each component requires an individually tailored mold, and the components are limited to the mold space.
In mechanically joined metal-plastic hybrid joints, on the other hand, the force transmission between the two joining partners is often unfavorable, leading to local stress peaks in the loaded component. The use of adhesives introduces an additional, sometimes cost-intensive material component into the process, usually leads to significantly longer process times and requires specially trained personnel. This situation necessitates the development of productive and cost-effective joining processes for metal-plastic hybrid joints, which is also reflected in the currently very lively research activity in this field.
Objective
The objective of the research project is to develop processes for the productive joining of metal-plastic hybrid joints using industrially available surface pretreatment techniques. The strengths of these joints should be able to compete with alternative joining methods, especially adhesive bonding. This includes thermal shock resistance. Due to the current economic and political importance of lightweight automotive construction, metal-thermoplastic combinations relevant in this area are being considered as a priority. Based on the results of the planned research project, recommendations for action are to be developed which will be useful in the future design of hybrid components.
Solution
An innovative approach to producing metal-plastic hybrid joints is direct thermal joining, in which metal and plastic are heated locally and joined in a manner comparable to welding processes. The work carried out to date in this field suggests that the process is likely to be industrially feasible, provided that suitable process sequences can be found for specific metal-plastic combinations.
The expected advantages of direct thermal joining are short cycle times, extensive possibilities for process monitoring and a high level of automation, which means that the process can be classified as very economical overall. In addition, thermal direct joining and the reverse process of "dejoining" that can also be implemented with it promise not only the development of innovative repair concepts but also separation of materials by type at the end of the component's life, making it compatible with the cycle economy targeted by the EU, unlike most alternatives in multi-material lightweight construction.
Overall, direct thermal joining thus has the potential to develop into a sustainable joining process for metal-plastic hybrid joints that can be used in both series and individual production. Specifically, the research project will focus on joining processes based on induction and ceramic high-rate heating elements, which are characterized by particularly fast heating cycles and can be applied as a thermal spray coating to a wide variety of geometries. Hybrid joining via induction is based on the Joule effect, which can heat up the metallic joining partner locally within a few seconds, thus enabling very fast process times. To create more planar joining zones, ceramic high-rate heating elements can be used, which are characterized by simplified geometric adaptation and the combination of joining pressure application and heating/cooling.
Procedure
In addition to characterizing the plastics and metals to be joined, the project will also characterize the various pretreatments to be considered and their influence. In subsequent parameter studies on thermal direct joining with short process times, the resulting joints are evaluated with regard to their mechanical strength and durability under static and dynamic climatic conditions. The resulting interrelationships between material properties, pretreatment influences, strength and climatic resistance will be analyzed and the results made available to companies and the public. The project itself also includes the further development of adapted ceramic high-rate heating elements as a cost-effective alternative to inductive heating sources.