Das Verbundprojekt »H2GO« soll die Produktion mobiler Brennstoffzellen revolutionieren
Kohlenstoff statt Gold: Auf dem Weg zum abgasfreien Schwerlastverkehr
Leistungsstarke mobile Brennstoffzellen sollen künftig helfen, die Umweltbelastung durch Schwertransporte in Deutschland und weltweit zu mindern. 19 Fraunhofer-Institute aus neun Bundesländern haben sich daher zum Entwicklungsbündnis »H2GO – Nationaler Aktionsplan Brennstoffzellen-Produktion« zusammengetan. Sie wollen gemeinsam industrielle Technologien für die effiziente Produktion von Brennstoffzellen entwickeln und neue Verfahren in die Wirtschaft transferieren. Im Fokus stehen Brennstoffzellen für den straßengebundenen Schwerlastverkehr. Das Bundesministerium für Digitales und Verkehr fördert H2GO bis Ende 2025 mit rund 80 Millionen Euro aus dem »Zukunftsfonds Automobilindustrie«. Auch das Fraunhofer-Institut für Werkstoff- und Strahltechnik IWS ist Teil dieses Konsortiums. Dr.-Ing. Teja Roch betreut innerhalb des Fraunhofer IWS das Teilprojekt »HP2BPP«. Im Interview erläutert er die innovativen Beiträge des Fraunhofer IWS.
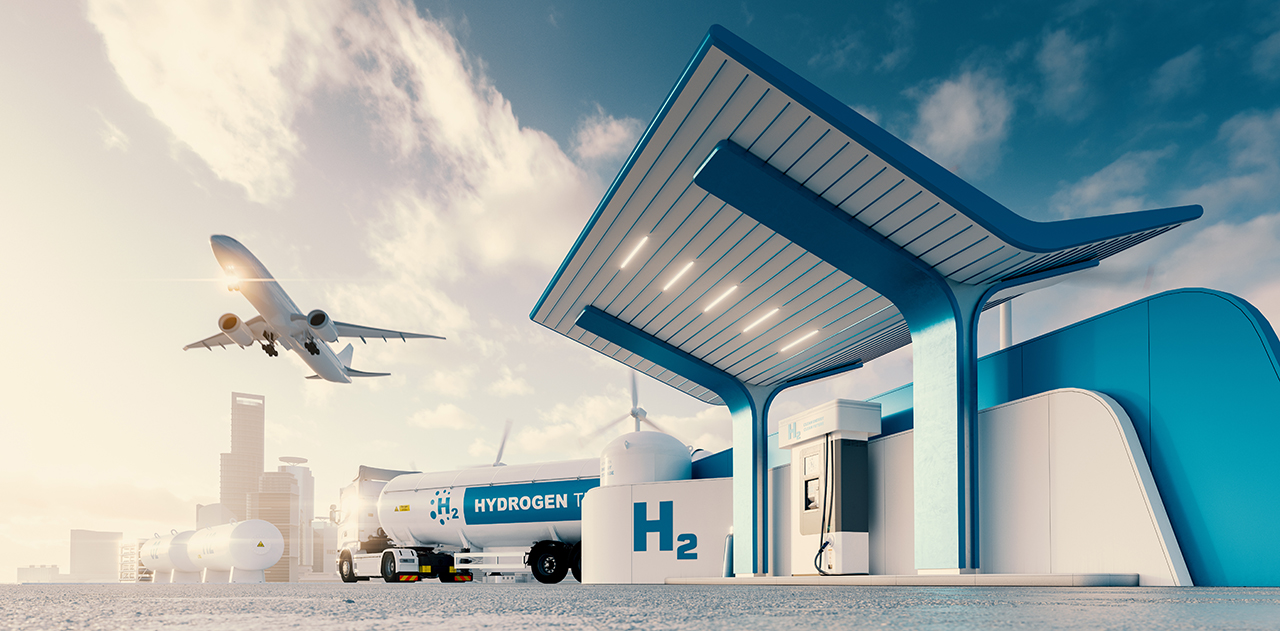
Brennstoffzellen bestehen aus vielen Bauteilen. Auf welche Komponenten und Prozesse konzentrieren Sie sich im H2GO-Verbund?
Dr. Teja Roch: Wir arbeiten gemeinsam mit weiteren Fraunhofer-Instituten unter anderem an Anlagen, die Bipolarplatten für Brennstoffzellen im Rolle-zu-Rolle-Verfahren besonders schnell und effizient fertigen können. Solche Bipolarplatten gehören zu den Schlüsselkomponenten von Brennstoffzellen-Stacks: Neben weiteren Funktionen werden über Kanäle Wasser- und Sauerstoff eingeleitet und verbinden die Zellen elektrisch. Für ihre Herstellung sind bisher kaum kontinuierliche Fertigungsverfahren etabliert. Die Platten müssen aus Metallblechen umgeformt und zugeschnitten werden. Je zwei Hälften werden dann zusammengefügt und beschichtet, um sie später mit weiteren Komponenten zu Stacks zu stapeln. Wir wollen diese Fertigungsprozesse stärker automatisieren sowie beschleunigen und setzen dabei auch neue Beschichtungsmaterialien ein.
Wie können wir uns diese neue Anlagengeneration vorstellen, wenn sie in den nächsten Jahren zur Serienreife kommen?
Dr. Teja Roch: Der Ablauf ist etwa Folgender: Ein Edelstahlband gelangt im Endlosbetrieb von einer Rolle durch Luft-Vakuum-Schleusen in die Beschichtungsanlage mit mehreren Kammern für die Physikalische Gasphasenabscheidung (PVD). Der Stahl wird zunächst gereinigt und mit einer metallischen Korrosionsschutzschicht beschichtet, die auch die Haftung verbessert. In einer weiteren PVD-Kammer wird eine leitfähige Kohlenstoffschicht auf das Band appliziert. Danach folgen Umformprozesse, durch den unter anderem die Kanäle für die Gasflüsse in das bereits beschichtete Band geprägt werden. Im Anschluss separiert die Anlage das Metallband in einzelne Platten und fügt diese paarweise zusammen.
Eine Neuerung stellt unter anderen die nur wenige Nanometer dicke leitfähige Schicht aus Kohlenstoff dar. Hierdurch können alternative dickere Schichten oder Edelmetallbeschichtungen z. B. aus Gold ersetzt werden. Dieser Ansatz hat das Potenzial, die Produktionskosten für Brennstoffzellen deutlich zu senken und den elektrischen Wirkungsgrad sogar noch zu erhöhen. Für den Korrosionsschutz erproben wir unter anderem eine Chrom-Schicht, aber auch andere Schichten aus Titan oder speziellen Legierungen.
Welche Aufgaben hat dabei konkret das Fraunhofer IWS im Zuge von H2GO übernommen?
Dr. Teja Roch: Wir konzentrieren uns im Teilprojekt HP2BPP einerseits auf die Beschichtungsverfahren und die dafür benötigten Prozesse, anderseits auf das Fügen, sei es nun durch Kleben oder durch Laserschweißen sowie das Austrennen der Bipolarplatten. Um andere Teilschritte wie beispielsweise das Umformen kümmert sich unter anderem das Fraunhofer-Institut für Werkzeugmaschinen und Umformtechnik IWU, das zugleich Konsortialführer ist.
Welcher Stand ist inzwischen erreicht und wo wollen Sie hin?
Dr. Teja Roch: In den vergangenen Monaten haben wir erhebliche Fortschritte bei der Prozessauslegung für die Bipolarplatten beim Beschichten, Fügen und Trennen erzielt. Wir haben beispielsweise für 100 Mikrometer dünne und 300 Millimetern breite Stahlbänder ein Anlagenkonzept zur Beschichtung erarbeiten, dass sich in der Realisierung befindet. Perspektivisch wollen wir 50 bis 75 Mikrometer dünne und auch breitere Bänder bei höheren Geschwindigkeiten bis zum Beispiel 60 Meter je Minute kommen. Weiterhin haben wir die grundlegende Machbarkeit innovativer Fügeverfahren mittels Laserspaltschweißen und Dichtklebens nachgewiesen und Anlagenkonzepte erarbeitet, die sich in der Umsetzung befinden. Damit solche Anlagen einen echten Mehrwert für die Anlagenbauer bieten, wollen wir sie grundsätzlich bis zu einer Taktrate von mehr als einer Bipolarplatte pro Sekunde hochtreiben.
Welche Herausforderungen sind auf dem Weg dahin zu meistern?
Dr. Teja Roch: Neben dem Anlagendesign im Ganzen sind viele Detailaufgaben zu lösen. Ein Beispiel ist die Auslegung der Kohlenstoff-Verdampfer für die PVD-Kammern. Dafür haben wir inzwischen ein Linear-Verdampfer Konzept entwickelt, verbessern aber auch als Alternativlösung fortlaufend etablierte Konzepte wie das Laser-Arc-Verfahren. Das Thema Verdampfer wird uns noch im gesamten Jahr 2024 und darüber hinaus beschäftigen. Große Fortschritte zeichnen sich im Übrigen bei den laserbasierten Fügeverfahren ab, die wir einsetzen, um aus je zwei Halbschalen eine Bipolarplatte zusammenzusetzen. Hierfür müssen wir beispielsweise Mehrstrahllaseroptiken auf kleinsten Bauräumen realisieren. Darüber können wir womöglich schon bald noch einige Neuigkeiten berichten.
Außerdem arbeiten wir weiter an besseren Luft-Vakuum-Schleusen, die einen kratzerfreien Übergang in die Vakuumkammern sichern müssen. Außerdem drehen wir immer noch an vielen Stellschrauben, um unsere Prozessgeschwindigkeit weiter zu erhöhen, die Qualitätssicherung inline realisieren und in Zukunft insgesamt smarte Prozesse anbieten zu können.
Warum ist H2GO so wichtig?
Dr. Teja Roch: Wir entwickeln hier die Fertigungstechnik von morgen und übermorgen. Wenn Produzenten in Zukunft kompakte Brennstoffzellen für den mobilen Einsatz preiswerter und effizienter produzieren können, dann wird dies auch dazu beitragen, dass Spediteure und andere Flottenbetreiber Lastkraftwagen mit solchen umweltfreundlichen Antrieben einsetzen. Damit würden wir dem Ziel eines abgasarmen oder sogar abgasfreien Schwerlastverkehrs ein wichtiges Stück näherkommen.
Ist das Verfahren allein für Hersteller von Brennstoffzellen interessant oder zeichnen sich auch andere Anwendungsfelder ab?
Dr. Teja Roch: Wir dürfen nicht vergessen, dass Bipolarplatten nicht nur für Brennstoffzellen gebraucht werden: Die Technologie könnte in Zukunft auch die Serienproduktion von Elektrolyseuren posititv beeinflussen und deren Kosten senken.
Dr. Teja Roch hat Physik an der TU Dresden studiert und zur Nanostrukturierung amorpher Kohlenstoffdünnschichten promoviert. Am Fraunhofer IWS leitet er die Projektgruppe im Dortmunder »OberflächenCentrum DOC®«.
Video: Kosteneffiziente Bandprozesse für die Herstellung von Bipolarplatten für Brennstoffzellen (CONTIbip)
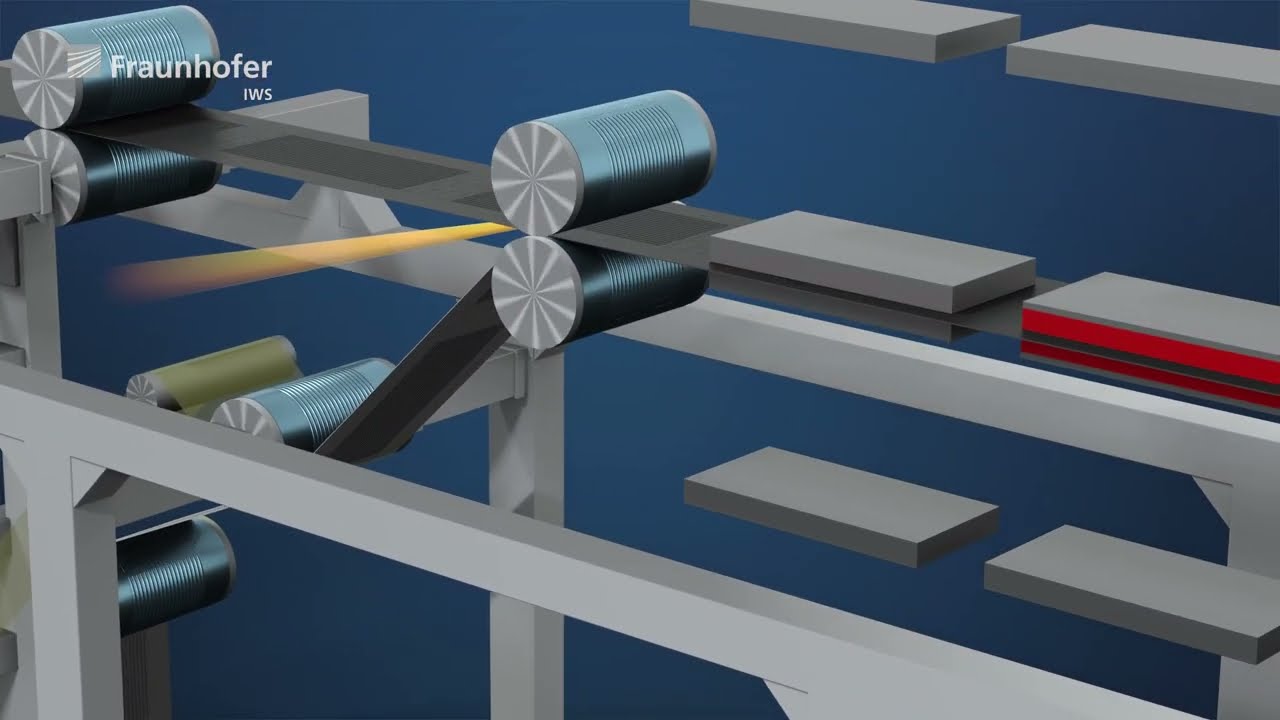
Datenschutz und Datenverarbeitung
Wir setzen zum Einbinden von Videos den Anbieter YouTube ein. Wie die meisten Websites verwendet YouTube Cookies, um Informationen über die Besucher ihrer Internetseite zu sammeln. Wenn Sie das Video starten, könnte dies Datenverarbeitungsvorgänge auslösen. Darauf haben wir keinen Einfluss. Weitere Informationen über Datenschutz bei YouTube finden Sie in deren Datenschutzerklärung unter: https://policies.google.com/privacy© Fraunhofer IWS